Резьбонарезание
Классификация резьбы
Резьба и резьбовые соединения широко распространены в технике. К их достоинствам относятся универсальность, надёжность, удобство сборки и разборки, простота изготовления. Классифицируем резьбы по наиболее характерным признакам. На рис. 1.22 показана схема классификации резьбы.
Резьбы подразделяются в зависимости от формы профиля на резьбы треугольного, прямоугольного, трапецеидального, круглого и других профилей; в зависимости от вида поверхности, на которой нарезана резьба, они классифицируются на цилиндрическую резьбу, расположена на поверхности цилиндра вращения, коническую – на поверхности конуса вращения, глобоидную – на поверхности гиперболоида вращения; в зависимости от расположения резьбы на поверхности стержня или в отверстии они подразделяются на наружные и внутренние.
|
|




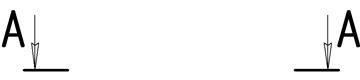

Рис. 1.21 Трёхзаходный винт прямоугольного профиля
По эксплуатационному назначению резьбы подразделяются на резьбы общего назначения и специальные. В свою очередь, резьбы общего назначения делятся на крепёжные (метрическая, дюймовая), крепёжно-уплотнительные (трубные, конические) и кинематические-ходовые (трапецеидальные, упорные, прямоугольные). К специальным резьбам относятся резьбы со стандартным профилем, но нестандартным диаметром или шагом.
Кроме того, все резьбы разделяют на две группы:
− стандартизованные резьбы, т.е. резьбы с установленными стандартами параметрами: профилем, шагом и диаметром;
− нестандартизованные резьбы, параметры которых не соответствуют стандартизованным.
По числу заходов резьбы подразделяются на однозаходные и многозаходные.
В зависимости от направления винтовой поверхности различают правые и левые резьбы.
|
Способы формообразования винтовых поверхностей на деталях можно классифицировать по виду обрабатывающих инструментов. На рисунке 2.1 представлена классификация способов изготовления винтовых поверхностей на деталях. Выбор способа изготовления деталей с винтовой поверхностью зависит от материала (металл, пластмасса, стекло и др.), от требований к условиям работы.
![]() |
Рис. 2.1 Классификация способов изготовления винтовых поверхностей на деталях
Широко распространённым способом изготовления резьбовых деталей в технологических процессах является резьбонарезание. С помощью резьбовых резцов и гребенок на токарно-винторезных станках выполняется нарезание резьбы как наружной, так и внутренней (для внутренней резьбы, начиная с d = 12 мм и выше). Этот способ характеризуется относительно невысокой производительностью, поэтому в настоящее время он применяется в основном в мелкосерийном и индивидуальном производстве, а также при создании точных винтов, калибров, ходовых винтов и т.д. Достоинство его – простота режущего инструмента и сравнительно высокая точность получаемой резьбы.
Процесс нарезания резьбы резцом осуществляется за несколько проходов, число которых зависит от шага и высоты профиля резьбы и ряда других факторов.
Схематически способ нарезания резьбы резцом показан на рисунках: 1.1 – 1.4, 1.7, т.е. заключается в следующем: при одновременном вращательном движении детали, на которой вырезается резьба, и поступательном движении резца (вдоль оси детали) последний снимает (вырезает) часть поверхности детали в виде винтовой линии.
При нарезании ходовых резьб, особенно с крупным профилем, зачастую используют два резца для получения резьбы нормального профиля.
Процесс нарезания резьбы многозубой гребенкой в сравнении с нарезанием резцом является более производительным. Гребенка, рабочая часть которой состоит из 5-8 зубьев, имеет по порядку различную высоту зубьев, последние из которых являются калибрующими и имеют полный профиль.
Работа по нарезанию распределяется между несколькими зубьями гребенки, благодаря чему сокращается число проходов и уменьшается время на обработку (рис. 2.2).
Рис. 2.2 Нарезание резьбы гребенкой
Нарезание крепежной резьбы в условиях серийного и массового производства производиться на токарных, револьверных и специальных станках при помощи плашек, резьбонарезных головок и метчиков.
Наиболее употребительные резьбонарезные инструменты:
плашки – для нарезания резьбы на стержнях (болт, винт, шпилька и др.), т.е. наружной резьбы (рис. 2.3). По своим конструктивным особенностям плашки делятся на круглые (лерки) и раздвижные (клупповые).
метчики– для нарезания внутренней резьбы в гайках, в отверстиях с резьбой (рис. 2.4).
Рис. 2.3 Плашка круглая (лерка)
Метчик представляет собой стальной стержень с нарезанной на нем резьбой и разделенный продольными прямыми или винтовыми канавками, образующими режущие кромки. Эти же канавки служат для выхода стружки. По способу применения метчики разделяются на ручные и машинные. Нарезают резьбу комплектом из двух или трех метчиков (малого, среднего и нормального чистового) в зависимости от ее размера. Для метрической с крупным шагом и дюймовой резьбы комплект состоит из трех метчиков, для метрической с мелким шагом и трубной резьбы – из двух.
В виду устройства резьбонарезного инструмента (например: плашки; метчика) или при отводе резца (рис. 2.5), при переходе от участка поверхности с резьбой полного профиля (участка l) к гладкой поверхности образуется участок длиной (l1) с постепенно уменьшающимся по высоте профилем.
Рис. 2.4 Метчик
Этот участок (l1) с неполноценной резьбой называется сбегом резьбы. Подобный сбег образуется и на конце глухого отверстия с резьбой, при применении метчика, у которого заборная часть имеет форму конуса (рис. 2.4, 2.7). Если резьбу выполняют до некоторой поверхности, не позволяющей доводить инструмент до упора к ней, то образуется недовод резьбы. Сбег и недовод образуют недорез резьбы (рис. 2.5). Если требуется изготовить резьбу на стержне полного профиля, то для вывода резьбонарезного инструмента делают проточку шириной b, диаметр d2, которой меньше внутреннего диаметра d1 резьбы (рис. 2.6).
Рис. 2.5 Наружная резьба
Для изготовления резьбы полного профиля в отверстии делают проточку шириной b1, диаметр d3, которой больше номинального диаметра резьбы d (рис. 2.8).
Обычно до нарезания резьбы на конце стержня и в отверстии делают фаску предохраняющую крайние витки от повреждений и являющуюся направляющей в резьбовом соединении (рис. 2.6 – 2.8). Размер l0 показывает положение проточки от торца детали (рис. 2.8).
Рис. 2.6 Нарезание полного профиля резьбы на стержне
|
Рис. 2.7 Резьба в глухом отверстии
Размеры фасок, сбегов, недорезов и проточек стандартизованы (ГОСТ 10549-80*, ГОСТ 27148 - 86 Изделия крепёжные. Выход резьбы, сбеги, недорезы и проточки. Размеры).
Рис. 2.8 Резьба полного профиля в отверстии
Последовательность изготовления глухого отверстия в детали сверлом и его условное изображение на чертежах показано на рис. 2.9. В начале сверлом высверливают гнездо, глубина которого зависит от пластичности материала, куда в дальнейшем будет ввернута деталь (шпилька, винт…).
Рис. 2.9 Нарезание глухого отверстия сверлом
Диаметр сверла должен быть выбран из таблицы стандартов в зависимости от нарезаемой в дальнейшем резьбы. Диаметр отверстия d1 равен диаметру сверла, которым это отверстие высверливается, L – глубина сверления отверстия.
Рис. 2.10 Нарезание резьбы метчиком в глухом отверстии
Способ изготовления глухого резьбового отверстия метчиком и его условное изображение показано на рис. 2.10. Следует знать, что под завернутой шпилькой или винтом остается незаполненная часть гнезда. Эта нижняя часть гнезда имеет запас полной резьбы, резьбу неполного профиля – сбег из-за нижней заборной части метчика и не нарезанную часть. Фаска в гладком отверстии выполняется до нарезания резьбы метчиком. Номинальный диаметр резьбы d равен диаметру метчика, l – полная глубина отверстия, l0 – длина полного профиля резьбы.