Рабочие чертежи стаканов и крышек подшипниковых узлов
Стаканы применяются для самостоятельного сборочного комплекта
с фиксирующими опорами (рис. 3.14). Наиболее часто стаканы используют
в конических передачах, где требуется точная установка и регулирование относительного положения зубчатых колес. Кроме того, установка стаканов необходима в подшипниковых узлах быстроходных валов червячных редукторов и цилиндрических вертикальных редукторов с неразъемным корпусом в случае, если диаметр выступов червяка или шестерни окажется больше диаметра наружного кольца подшипника da1 > D. Стаканы изготавливают обычно из чугуна СЧ15-32, реже из стали.
Толщину стенок dслитых стаканов из чугуна марки СЧ15-32 выбирают в зависимости от диаметра наружного кольца подшипника в соответствии с данными, приведенными ниже:
диаметр отверстия для стакана или крышки | < 50 | 50-62 | 63–95 | 100 -145 | 150-220 |
толщина стенки стакана d, мм | 4…5 | 5–7 | 7 -9 | 9 -11 | 11 -13 |
толщина стенки крышки dк,мм | |||||
диаметр винта d, мм | |||||
число винтов z |
Толщина фланца d2 ≈ 1,2 d
Наружный диаметр стакана Dc » D + 2dс округляют до ближайшего стандартного числа по ГОСТ 6636–69 из ряда Rz 40. Толщину упорного буртика d1 принимают равной толщине d стенок. Высоту t упорного буртиканазначают в соответствии с размером подшипника качения. Если осевая сила направлена в сторону, противоположную бурту, то можно использовать более технологичную конструкцию стакана с пружинным кольцом, заменяющим бурт.
Диаметр и количество винтов для крепления стаканов принимают в зависимости от диаметра стакана или крышки. Диаметр фланца выполняют минимальным (рис.3.14)
где d – диаметр винта.
в |
г |
б |
а |
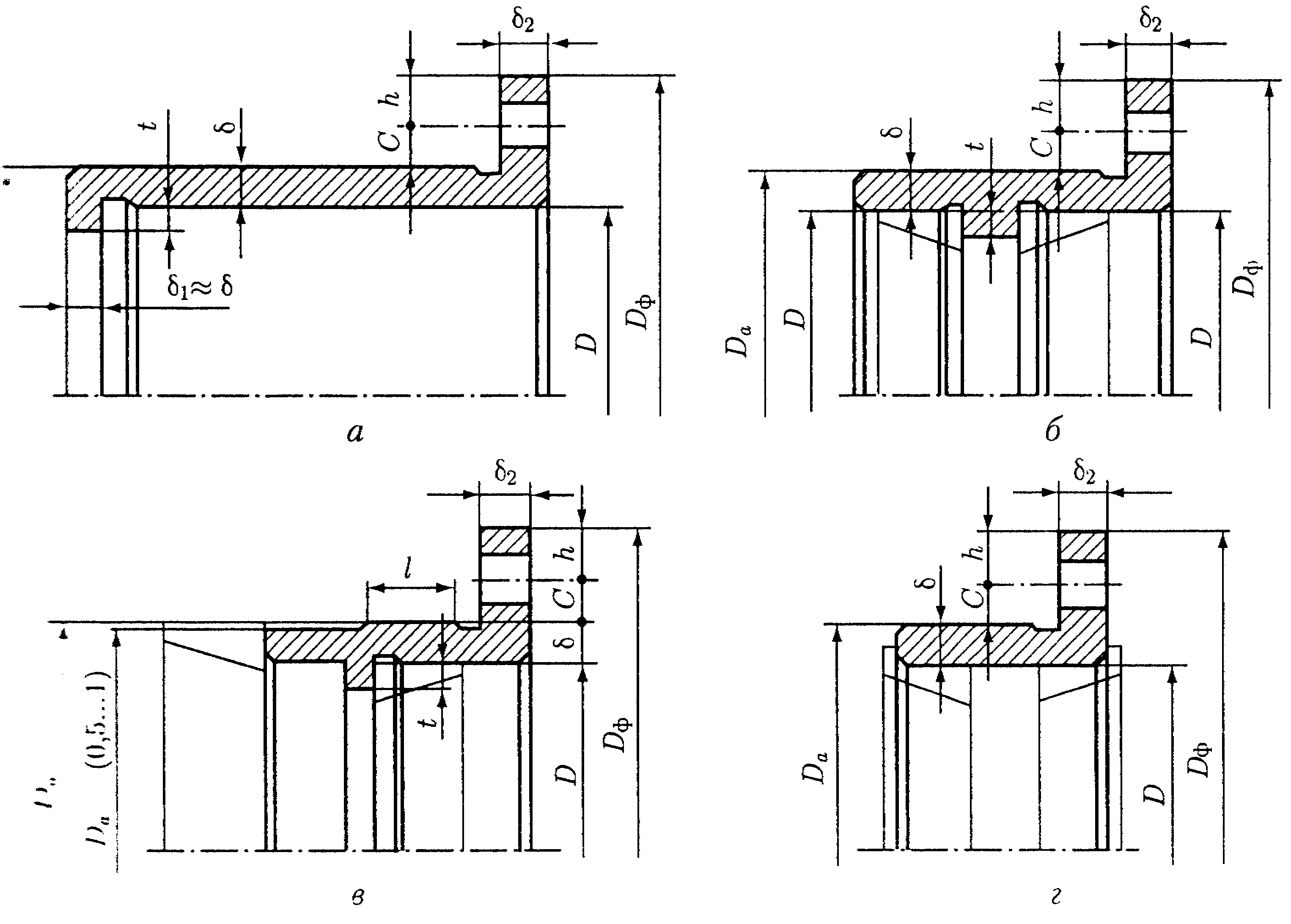
Рис. 3.14. Конструкция стаканов
Для снижения массы корпуса допускается свисание стакана b » (1,5–2,0) d. Проточка, выполненная на наружной поверхности стакана, облегчает сборку и уменьшает длину шлифуемой поверхности. Если стакан в процессе сборки неоднократно перемещают вдоль оси отверстия, то предусматривают посадку H7/h6 или H7/j6. Более надежной является посадка H7/k6, которая может быть применена в том случае, если регулирование осевого положения стакана не требуется.
На чертежах стаканов (рис.3.15, а, б) задают осевые линейные размеры: габаритные, цепочные и свободные. Предельные отклонения задают на размеры: свободные - среднего класса точности; цепочные - по общему правилу (см. выше).
Допуски формы и допуски расположения поверхностей приведены
в табл. 2.2.
Таблица 3.10
Позиция на рис. 3.15 | Допуск |
1 2 3 4 5 6 | Т/0/ » 0,5t, где t – допуск размера поверхности Тã » 0,6 t, где t – допуск размера поверхности Тã по табл. 3.2 в зависимости от типа подшипника Т^ – на диаметре D по табл. 3.5. Степень точности допуска для подшипников: шариковых – 8, роликовых – 7 Т// на диаметре Dф по табл. 3.5.Степень точности допуска для подшипников качения: шариковых – 8, роликовых – 7 Т+ » 0,4(dотв – dв), где dотв– диаметр отверстия, dв – диаметр винта |
Рис. 3.15.Примеры чертежей стаканов
Основной базой является поверхность В фланцев стакана. Точность положения базовых торцов стакана для упора подшипников обеспечивает их параллельность торцу В стакана.
Назначение каждого из допусков (рис. 3.15):
допуск цилиндричности(поз. 1) задают, чтобы ограничить отклонение геометрической формы посадочных поверхностей и связанных с ними дорожек качения наружных колец подшипников;
допуск соосности посадочных поверхностей стакана назначают, чтобы ограничить отклонение межосевого расстояния в конической передаче (поз. 2) и перекос колец подшипников качения (поз. 3);
допуск перпендикулярности (поз. 4) и допуск параллельности (поз. 5) задают, чтобы ограничить перекос колец подшипников;
позиционный допуск (поз. 6) задают, чтобы ограничить отклонение
в расположении центров крепежных отверстий и обеспечить так называемую «собираемость» резьбового соединения. Этот допуск задают только в том случае, когда отверстия для винтов в стакане и в корпусной детали сверлят независимо друг от друга в приспособлениях или на станках с ЧПУ. В остальных случаях позиционный допуск не приводят.
Пример рабочего чертежа стакана приведен в прил. 3 (рис. П.3.5).
Крышки подшипниковых узлов. Привертныекрышки применяютсяв неразъемных корпусах для подшипниковых узлов, а также в редукторах с разъемными корпусами.Крышки подшипников изготовляют из чугуна марок СЧ15, СЧ20. Конструкции привертных крышек приведены на рис. 3.16. Они могут быть глухими рис. 3.16, а, б, г и с отверстием под выходной вал (рис. 3.16, в). Выбор конструкции крышки зависит:
- от уплотнения выходных валов(см. уплотнения валов);
- крепления подшипников на валу (если вал не выходит за пределы подшипника, то крышку выполняют с плоской внешней поверхностью (рис. 3.16, а, б)
- если торец вала выступает за пределы подшипника, то крышку выполняют по рис.3.16, г);
- регулировки зазора подшипника, которая производится установкой набора прокладок под фланец крышки (см. рис. 3.16) или воздействием винтами с резьбовыми крышками (см. рис.2.43);
- размещения комплекта деталей подшипникового узла.
При размещении комплекта в корпусе редуктора крышка выбирается по диаметру наружного кольца подшипника D, если комплект деталей собирается в стакане, то размеры крышки определяют по его наружному диаметру.
Ниже приведены рекомендации по выбору толщины стенки, диаметра d и числа z винтов крепления крышки к корпусу в зависимости от D:
D | 50–62 | 63–95 | 100–145 | 150–220 |
d | ||||
d | ||||
z |
а |
б |
в |
г |

Рис. 3.16. Крышки подшипниковых узлов
В варианте по рис. 3.16, б крышку крепят винтами с цилиндрическими головками и шестигранным углублением под ключ. В этом случае толщину крышки принимают
d3 = Н + 0,8 d,
где Н – высота головки винта.
Опорные поверхности под головки крепежных болтов или гаек чаще всего необходимо обрабатывать. Обрабатывают или непосредственно те места, на которые опираются головки винтов (рис. 3.16, а, б), или весь поясок на торце в зоне расположения головок винтов (рис. 3.16, в, г). Размеры других конструктивных элементов крышки: d1 = 1,2d; d2 = (0,9–1) d; Dф = D + (4… 4,4) d; С » d.
Закладные крышки.На рис. 3.17 показаны основные конструкциизакладных крышек: глухих – рис. 3.17, а, б; с отверстием для выходного конца вала рис.3.17,в; с резьбовым отверстием под нажимной винт – рис. 3.17,г. Закладные крышки широко применяют в редукторах, имеющих плоскость разъема по осям валов. Эти крышки не требуют крепление к корпусу резьбовыми деталями: их удерживает кольцевой выступ, для которого в корпусе протачивают канавку. Чтобы обеспечивать сопряжения торцов выступа крышки и канавки корпуса по плоскости, на наружной цилиндрической поверхности крышки перед торцом выступа желательно выполнять канавку шириной b. Размер канавки на диаметре D принимают равным D = d.
Наружный диаметр крышки выполняют с такими отклонениями, при которых в сопряжении с корпусом образуется малый зазор, препятствующий вытеканию масла из корпуса. Толщину d стенки принимают в зависимости от диаметра D отверстия под подшипник (см. выше). Размеры других элементов крышки: d1 = (0,9–1) d; S = (0,9–1) d; С » 0,5S; l ³ b.
в |
г |
б |
а |

Рис. 3.17.Закладные крышки подшипниковых гнезд
На чертежах крышек подшипников осевые размеры проставляют по рис.3.18. Во всех конструкциях размер S получен при отливке крышки на заготовительной операции. Размер h обычно входит составляющим размером размерной цепи, определяющей осевой зазор в комплекте вала с подшипниками качения. Размер Н везде габаритный. Размер С связывает необработанные и обработанные поверхности, С0 – глубина гнезда для манжетного уплотнения.
Рис. 3.18.Предельные отклонения размеров
Рис. 3.19. Допуски расположения поверхностей
Предельные отклонения цепочного размера h располагают симметрично относительно номинального значения по рекомендациям (см. рис. 3.18). Поля допусков центрирующего пояска D и диаметра Dм под манжетное уплотнение принимают по рис. 3.18.
Допуск расположения поверхностей принимают по табл. 3.11 в соответствии с позициями, указанными на рис. 3.19.
Назначение каждого из допусков следующее:
допуск параллельности торцев (поз. 1) задают, если по торцу крышки базируют подшипник качения, как показано на рис. 3.19. Допуск назначают, чтобы ограничить перекос подшипников качения;
допуск соосности (поз. 2) задают, чтобы ограничить радиальное смещение уплотнительной манжеты и уменьшить таким образом неоднородность давления на рабочую кромку манжеты;
позиционный допуск (поз. 3) задают в тех случаях и с той же целью, как и на чертежах стаканов (см. поз. 6 на рис. 3.15).
Таблица 3.11
Позиция на рис. 3.19 | Допуск |
1 2 3 | Т// на диаметре Dф по табл. 3.5. Степень точности допусков при базировании подшипников: шариковых – 9 (привертная крышка) или 8 (закладная крышка): роликовых – 8 (привертная крышка) или 7 (закладная крышка) Тã » 0,6 t, где t – допуск размера поверхности Т+ » 0,4(dотв – dв), где dотв– диаметр отверстия; dв – диаметр винта |
Рабочий чертеж крышки приведен в прил. 3 (рис. П.3.6).