Электрофильтры
Метод электроосаждения (улавливания пыли в электрическом поле) заключается в следующем. Частицы пыли (или капельки влаги) сначала получают заряд от ионов газа, которые образуются в электрическом поле высокого напряжения, а затем движутся к заземленному осадительному электроду. Попав на заземленный уловитель, частицы прилипают и разрежаются. Когда осадительный электрод накапливает слой частиц, последние стряхиваются под воздействием вибрации и собираются в бункер. Схема электрического осаждения пыли представлена на рис. 5.7.
Рис. 5.7. Схема электрического осаждения пыли: 1 - источник электропитания; 2- коронирующий электрод; 3 - осадительный электрод; 4 - ион газа; 5 - частица пыли.
Электрофильтры применяются там, где необходимо очищать большие объемы газа и отсутствует опасность взрыва. Эти установки (рис.5.8) используются для улавливания летучей золы на современных электростанциях, пыли в цементной промышленности, а также в металлургии - в мощных системах улавливания дыма, в системах кондиционирования воздуха и других смежных отраслях [2].
Рис. 5.8.Двухступенчатый электрофильтр горизонтального потока:
1- комплект стряхивателей для высоковольтных и собирательных электродов; 2- отдельная сблокированная дверца смотрового люка; 3 – открывающиеся панели для извлечения проволочных электродов без отключения установки; 4- распорные стержни между осадительными электродами; 5 - дырчатый распределительный экран; 6 - станина, устанавливаемая непосредственно на опорных колоннах; 7 - блокированное высоковольтное оборудование для каждой электрической секции; 8- площадка для размещения изоляторов и газонепроницаемых уплотнителей; 9 - скатная крыша; 10 - клиновидные опоры для проволочных электродов; 11 - упруго закрепленные собирательные электроды; 12- пластинчатые и щитковые электроды; 13- упруго закрепленная высоковольтная рама; 14 - люк смотрового прохода между ступенями.
4. Аппараты "мокрого" пыле-, газоулавливания
При очистке газов от частиц пыли и переработке газообразных отходов, с целью извлечения из них полезных компонентов или их обезвреживания, успешно применяют методы и оборудование, основанные на принципах мокрого пылеулавливания. Целесообразно сочетание сухой и последующей мокрой очистки, которая в свою очередь может сочетаться с адсорбционной доочисткой.
Развитая поверхность контакта фаз способствует увеличению эффективности пылеулавливания. В промышленности используют мокрые пылеуловители (промыватели) капельного, пленочного и барботажного типов. Конструктивно аппараты могут быть полыми, тарельчатыми, механического и ударно-инерционного действия (ротоклоны), а также скоростного типа (трубы Вентури и другие инжекторы).
Эффективность очистки пыли зависит от размеров улавливаемых частиц и других свойств пыли. Необходимость концентрирования системы "жидкость - твердое тело" с возвратом очищенной воды на пылеулавливание, накопление в орошаемой жидкости растворимых компонентов пыли усложняет систему мокрого пылеулавливания.
В общем виде процесс улавливания пыли "мокрым" методом представляется как перенос твердой фазы из газовой среды в жидкую, и удаление последней из аппарата вместе с твердой фазой [2,3]. В зависимости от формы контактирования фаз способы мокрой пылеочистки можно разделить на:
1 - улавливание в объеме (слое) жидкости;
2 - улавливание пленками жидкости;
3 - улавливание распыленной жидкостью в объеме газа (рис.5.9).
Рис. 5.9. Схемы основных способов мокрого пылеулавливания:
а - в объеме жидкости; б - пленками жидкости; в - распыленной жидкостью;
1 - пузырьки газа; 2- капли жидкости; 3- твердые частицы.
Скрубберы (газопромыватели).
При объемно-жидкостном способе поток запыленного газа пропускают через определенный объем жидкости. Для этой цели используют пенные пылеуловители с провальными тарелками или тарельчатые скрубберы, эффективность которых может достигать 90-95%. На рис. 5.10 представлен тарельчатый скруббер.
Улавливание пыли пленками жидкости характеризуется тем, что контакт газа и жидкости происходит на границе двух сред без перемешивания. Захват твердых частиц тонкими пленками жидкости происходит на поверхности конструктивных элементов. К этой группе устройств относятся скрубберы с насадкой, мокрые циклоны, ротоклоны и т.п. На рис. 5.11 показана схема пылеуловителя вентиляционного мокрого (ПВМ).
|
|
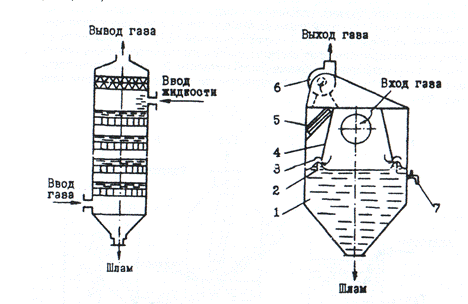
Улавливание пыли распыленной жидкостью заключается в том, что орошающая жидкость вводится в запыленный поток газа с помощью форсунок под давлением или за счет энергии самого потока газа. Первый способ распыления используется в полых скрубберах (рис.5.12), второй - в турбулентных промывателях - скрубберах Вентури (р и с. 5.13).
|
| ||||
Скрубберы Вентури (сочетание трубы с каплеуловителем центробежного типа) обеспечивают очистку газов от частиц пыли практически любого дисперсного состава. В зависимости от физико-химических свойств улавливаемой пыли, состава и температуры газа выбирают режим работы скруббера Вентури. Скорость газа в горловине может быть 30-200 м/с, а удельное орошение 0,1-6 м3/м3. Скрубберы Вентури эффективно работают при допустимой запыленности очищаемых газов 30 г/м3, предельной температуре очищаемого газа 400 °С, удельном орошении 0,5-2,5 м3/м3 и гидравлическом сопротивлении 6-12 кПа.
Характеристика труб типа ГВПВ (газопромыватель Вентури прямоточный высоконапорный) приведена в табл . 5.3. Конструкция часто дополняется каплеуловителем циклонного типа (КЦТ), который обеспечивает улавливание влаги при содержании жидкости ≤ 1 м3 / м3, температуре ≤ 80 °С, концентрации капельной влаги после сепарации 70 мг / м3. Гидравлическое сопротивление 350 Па, производительность КЦТ 1700-62500 м3 / ч.
Таблица 5.3
Технические характеристики скруббера Вентури
Типоразмер | Объем газов на выходе, м3/ч | Диаметр горловины, мм | Расход орошаемой жидкости, м3/ч | Давление жидкости перед форсункой, кПа |
ГВПВ-0,006 | 1700-3500 | 1,18-3,2 | 180-370 | |
ГВПВ-0,03 | 9320-18900 | 6,5 | 60-250 | |
ГВПВ-0,08 | 23460-47600 | 16,8-45 | 80-570 | |
ГВПВ-0,140 | 41400-84000 | 28,8-46 | 130-320 |
Скрубберы Вентури типа СВ-Кк (комплект: скруббер-сепаратор, один или два) имеют следующие характеристики:
Объем очищаемых газов, м3/ч – 50 000-500 000
Расход орошаемой жидкости, м3/ч – 65-400
Температура очищаемых газов, °С – до 120
Концентрация взвешенных частиц, мг/м3 – до 10 000
Удельное орошение, м3/м3 – 0,5-3,5
Гидравлическое сопротивление, кПа – 4-12
Созданы скрубберы центробежные, вертикальные, батарейные СЦВБ-20, обеспечивающие производительность по газу 9 000-20 000 м3/ч при температуре не выше 60 °С, запыленности не более 10 г / м3 и гидравлическом сопротивлении скрубберов 1,7 кПа. Мокрую очистку газов с частицами 2-3 мкм можно проводить в скрубберах центробежного типа СЦВП, в которых жидкость дробится непосредственно запыленным газом. Шлам, оседающий в нижней части скруббера, выводится эрлифтом в контейнер, а осветленная жидкость вновь возвращается в скруббер. Производительность таких аппаратов составляет 5 000-20 000 м3 /ч, допустимая запыленность 2 г / м3, температура газов 80 °С, гидравлическое сопротивление 2,4 кПа, расход воды на очистку 0,05 м3 / м3.
Разработаны скрубберы ударно-инерционного типа с пылеуловителями вентиляционными мокрыми. Производительность таких скрубберов 3 000-40 000 м3/ч. Запыленность газов 10 г/м3, гидравлическое сопротивление аппарата 0,8-2 кПа, расход воды 10-40 г на 1 м3 очищаемого воздуха.
Для химической очистки газов от соединений фтора с содержанием до 1 г / м3 можно рекомендовать скрубберы с шаровой подвижной насадкой и полые. Очистку проводят растворами гидроксида или карбоната натрия.
Эффективность очистки газов от пыли зависит от дисперсности, плотности, склонности к слипанию, сыпучести, абразивности, смачиваемости, гигроскопичности, растворимости и др. Однако основным параметром при выборе пылеуловителя является размер частиц. Необходимо знать дисперсный состав пыли, задаваемый в виде таблиц или интегральных кривых. Гранулометрический состав большинства видов пыли подчиняется нормальному логарифмическому закону распределения частиц. Степень очистки газов определяют по формуле:
(6)
где lg (dm / d50) / √ lg2 σr + lg2 ση;
dт – медианный диаметр частиц пыли, мкм;
d50 – диаметр частиц пыли, улавливаемых в аппарате на 50 %;
lg σr – стандартное отклонение в функции распределения частиц по размерам;
lgση – стандартное отклонение в функции распределения фракционных коэффициентов очистки.
С достаточной точностью дисперсию (геометрическое стандартное отклонение) можно рассчитать по формуле:
σ = d84 / dm = dm / d16 (7)
где d16, d84 – диаметр частиц с содержанием фракций < 16 и < 84 %, соответственно.
По номограмме (рис.14) определяют эффективность улавливания пыли в аппаратах мокрой очистки. График построен для значений dm и d50 пыли стандартной плотности ρг = 1000 кг / м3.
Пересчёт значений dm и d50 от реальной плотности ρг к стандартной проводят по формуле:
d50 (или dm) = d50* (или dm*) (8)
Зависимость степени пыле-, газоочистки от энергозатрат:
η = 1 – (9)
где Kr - удельная энергия соприкосновения, кДж / 1000 м3 газов;
b и k - константы, определяемые из дисперсного состава пыли, позволяют рассчитать эффективность улавливания пыли.
Рис.14. Номограмма для определения эффективности улавливания пыли в аппаратах мокрой очистки газов.
Вероятностно-энергетический метод расчета мокрых пылеуловителей основан на обобщенной зависимости
d50= 188, 32 Kr-0,645, (10)
полученной для стандартной плотности пыли ρг = 1000 кг / м3 и вязкости газов µr = 18 · 10-6 Па · с.
Эта зависимость может быть использована для выбора способов очистки и принципиальной конструкции скрубберов.
Пример:Дано: дисперсный состав пыли (dm и lgσг), плотность пыли ρг, вязкость газов µг и требуемая эффективность пылеулавливания η. Принимаем η = Ф(х) по таблицам и рассчитываем значение d50 .
(11)
Приводим d50 к стандартным условиям и рассчитываем значение Кг. Затем обращаемся к значениям Кг и lgσn, по которым выбирается тип скруббера:
где m – удельное орошение, м3/м3;
Рж - давление распыляемой жидкости, Па;
ΔРр - гидравлическое сопротивление в рабочей зоне скруббера, Па.
Если же необходимо оценить эффективность действующего скруббера, то, зная дисперсный состав пыли, ее плотность и вязкость газов, имея гидравлические характеристики работы скруббера (ΔРр, m и Рж), находим значение Кг и рассчитываем значение d50. Проводим корректировку до значения d50.
|
|
|
Рекомендации к выбору типа скруббера
Тип скруббера | Зависимости для расчета величины Кг | lg ση |
Полый | mРж | 0, 29 |
Насадочный | ΔРρ | 0, 21 |
Тарельчатый | ΔРρ | 0, 15 |
Ударно-инерционного действия | ΔРρ | 0, 29 |
Вентури | ΔРρ+ Рж | 0, 29 |
Далее с помощью приведенных выше зависимостей определяем х и значение Ф(х) по таблицам, что будет соответствовать значению эффективности пылеулавливания в данном скруббере.
Для очистки или обезвреживания газообразных отходов или технологических газов с целью извлечения из них сопутствующих (полезных) газообразных компонентов широко используют метод абсорбции.
Таблица 5.5
Абсорбенты, применяемые для очистки отходящих газов
Поглощаемые компоненты | Абсорбенты |
Оксиды азота N2O3, NO3 | Вода, водные растворы и суспензии: NaOH, Na2C03, NaHC03, КОН, K2C03, КНС03, Ca(OH)2, CaC03, Mg(OH)2, MgC03, Вa(ОН)2, BaC03) NH4HC03 |
Оксид азота NO | Растворы FeCl2, FeS04, Na2S203, NaHC03, Na2S03, NaHS03 |
Диоксид серы SO2 | Вода, водные растворы: Na2SO3 (18-25%-ные), NH4OH (5-15%-ные), Ca(0H)2 Na2C03 (15-20%-ные), NaOH (15-25%-ные), КОН, (NH4)2S03 (20-25%-ные), ZnS03, К2С03: суспензии CaO, МgО, СaС03) ZnO, золы; ксилидин - вода в соотношении 1:1, диметиланилин C6H3(CH3)2NH2 |
Сероводород H2S | Водный раствор Nа2СОз + Na3Аs04 (Na2HAs03); водный раствор As203 (8-10 г/л) + NН3 (1.2-15 г/л) + (NH4)3As03 (3,5-6 г/л); моноэтаноламин (10–15 %-ный раствор); растворы К3Р04 (40-50%-ный раствор); растворы К3Р04 (40-50%-ные), NH4OH, К2С03, CaCN2, натриевая соль антрахинондисульфокислоты |
Оксид углерода СО | Жидкий азот; медно-аммиачные растворы [Cu(NH3)]n x СОСН |
Диоксид углерода СO2 | Водные растворы Na2С03, K2C03, NaOH, КОН, Са(ОН)2, NH4OH, этаноламины RNH2, R2NH4 |
Хлор Сl2 | Растворы NaOH, КОН, Са(ОН)2| Na2C03, К2С03, MgC03, СаСO3 . Na2S203; тетрахлоридметан CCI4 |
Хлористый водород HCI | Вода, растворы NaOH, КОН, Са(ОН)2, Na2C03, К2СОз |
Соединения фтора HF, SiF4 | Na2C03, NaOH, Са(ОН)2 |
Процесс абсорбции основан на непосредственном взаимодействии газов с жидкостями. Различают физическую абсорбцию, т.е. растворение газа в жидкости; и хемосорбцию, в основе которой лежит химическая реакция между газом и жидким поглотителем.
![]() |
Абсорбционной очистке подвергают газообразные отходы, содержащие один или несколько извлекаемых компонентов. В зависимости от используемого абсорбента (табл.5.5)и его селективности можно выделить либо один компонент, либо последовательно несколько. В результате процесса абсорбции получают очищенный газ и насыщенный раствор, который должен быть легко регенерируемым с целью извлечения из него полезных газов и возвращения его в процесс.
Требования, которым должна удовлетворять абсорбционная аппаратура, вытекают из физического представления явлений массопереноса в системах газ - жидкость. Так как процесс массопереноса протекает на поверхности раздела фаз, то в конструкциях аппаратов необходимо ее максимально развивать.
Для поверхностных абсорберов характерным является конструктивно образованная поверхность, по которой в плёночном режиме стекает абсорбент (жидкость). Наиболее распространенной конструкцией таких противоточных абсорберов являются хорошо известные насадочные скрубберы. В качестве насадки применяют кольца Рашига, кольца Палля, седла Берля и др.
В распыливающих абсорберах межфазная поверхность образуется мелкими каплями путем дробления, распыления жидкости. В объеме аппарата с помощью форсунок создаются капли, контактирующие с газовым потоком.
В механических абсорберах жидкость распыляется в результате подвода извне механической энергии, например, вращения валков или специальных распылителей.
В поверхностных и распыливающих асорберах сплошной фазой является газ, а распределенной - жидкость. В барботажных абсорберах всплошном потоке жидкости распределяется газ, что достигается на так называемых тарелках. Режим, в котором работают такие абсорберы, называют барботажным.
При создании промышленных систем очистки газов абсорбционными методами необходимо различать схемы с одно- и многократным использованием абсорбента. В последней схеме абсорбция сочетается с десорбционными процессами. Однократное использование абсорбента характерно для процессов с низкой стоимостью поглотителя или когда после поглощения образуется готовый (целевой) продукт. Так как в очищаемом газе содержится незначительное количество улавливаемого компонента, то осуществляется циркуляция абсорбента, но без его регенерации.
Расчет процессов абсорбции основывается на материальном балансе, из которого определяют расходные параметры абсорбента и размеры аппарата. Объем очищаемого газа G1 известен, как и начальная концентрация поглощаемого компонента в газовом потоке у1 и в абсорбенте, подаваемом на очистку, х1. Необходимо знать конечную концентрацию х2 абсорбента, то есть степень насыщения потока абсорбента L поглощаемым компонентом. Тогда количество поглощаемого компонента Gk определяют по формуле:
Gk = G(y1 - y2), (13)
где у2 - концентрация компонента в отходящем газовом потоке. Общее уравнение материального баланса имеет вид:
G(y1 - y2) = L (x2 – x1). (14)
Конечное содержание поглощаемого компонента у2 в газовом потоке должно быть согласовано с равновесной концентрацией его в жидкости, которую определяют по формуле:
, (15)
где х- равновесная концентрация компонента в жидкости, отвечающая его содержанию в газовой фазе у2; т - константа фазового равновесия (константа Генри).
Определение эффективности реальных аппаратов можно выполнить, учитывая скорость растворения газа в жидкости за время контакта поверхности фаз F, м2:
Gk = dG/dτ = KFΔ (16)
Каждая из независимых переменных (Κ - коэффициент массопередачи и Δ - движущая сила процесса) зависят от многих параметров (технологического режима, конструкции аппаратов) и может измеряться в различных единицах. Широко применяют формулу для коэффициента массопередачи KS, как отношение его к площади поверхности контакта фаз или к площади насадки, тарелки. Если при этом движущая сила выражена через ∆, кг/м3, то KS - м/с.
Коэффициент массопередачи относят также к объему аппарата, получая объемный коэффициент массопередачи KV, с-1 или ч-1:
КV = К · а, (17)
где а - удельная поверхность контакта фаз.
Так как интенсивность переноса массы в газовой фазе (частный коэффициент массоотдачи βг) и в жидкой (частный коэффициент массоотдачи βж) различны, то значение βг и βж определяют по разным зависимостям. В этом случае выражение общего коэффициента массопередачи (через частные) имеет вид:
Ks = 1/(1/βг+ 1 / mβж) (18)
Соотношение между 1/βг и 1/mβж позволяет определить долю сопротивления в газовой и жидкой фазе в зависимости от m. Значения βг и βЖ находят по экспериментальным зависимостям, рекомендуемым для массообменных аппаратов.
В случае прямолинейной равновесной зависимости и постоянства βг и βж по высоте абсорбера количество переданной массы равно:
G (y1 - y2) = KS·F·Δ, (19)
или
(20)
Последнее выражение называют числом единиц переноса. По аналогии с записью коэффициентов массопередачи можно записать:
N = Nг + m · G · Nж / L, (21)
где Nг и Nж - число единиц переноса в газовой и жидкой фазах соответственно.
Число единиц переноса через объемные коэффициенты массопередачи:
N = KvVan / G = KV·S·H / G, (22)
где Van - объём аппарата; S - площадь поперечного сечения; Н - высота аппарата.
Тогда высота аппарата:
Н = N·G / KV·S, (23)
причем G/(KVS) отвечает высоте аппарата, для которого число единиц переноса равно единице (и называется высотой единицы переноса).
Число единиц переноса N можно определить графически. Площадь, ограниченная кривой на графике, соответствует общему числу единиц переноса, а угол ее наклона позволяет определить константы b и k, входящие в формулу 9.
Существенным недостатком сорбционных методов очистки (абсорбционных и адсорбционных) газов является необходимость многократной регенерации поглощающих растворов или частичной замены твердого сорбента, что значительно усложняет технологическую схему, увеличивает капитальные вложения и затраты на эксплуатацию.
5. Комбинированные методы очистки газов
Комбинированные методы очистки газов являются весьма экономичными и наиболее высокоэффективными. Рассмотрим конструкции аппаратов и технологическую схему очистки запыленного воздуха и газов стекольного производства.
Для обеспыливания аппаратов измельчения, просеивания, сушки, смешивания и транспортирования сырьевых материалов разработан гидродинамический пылеуловитель ГДП-М (рис.5.15) производительностью от 3 000 до 40 000 м3/ч. Принцип работы аппарата основан на пропускании запыленного воздуха (газа) через слой пены, образующейся на газораспределительной решетке, погружённой в пыле-смачивающую жидкость. Запыленный газ поступает в подрешёточное пространство и, вытесняя на решетку часть воды, образует на ней слой турбулентной пены. Пройдя через отверстия, газ очищается от пыли в момент контакта с жидкостью. Очищенный газовый поток поступает в центробежный каплеотделитель и затем выбрасывается в атмосферу. Пылеуловитель имеет следующие характеристики:
Производительность, м3/ч | 3 000-40 000 |
Удельная нагрузка по газу, м3/(м2 ·ч) | 6 500 |
Гидравлическое сопротивление, Па | 1 400-1 900 |
Температура очищаемых газов, °С | до 300 |
Расход воды на очистку 1000 м3 газа, л | 15-50 |
Установочный объем, м3 | 2,5 |
Масса, кг |
Аппарат ГДП-М обладает максимальной эффективностью очистки газов от мелкодисперсной пыли на 2-ой ступени (после циклонов).
Рис. 5.15. Гидродинамический пылеуловитель ГДГ1-М: 1-сходной патрубок; 2 - газораспределительная решетка; 3 - корпус; 4 - каплеотделитель; 5 - выходной патрубок; 6 - регулятор подачи воды; 7- разгрузочное устройство.
Рис.5.16. Схема очистки технологических выбросов: 1 - железнодорожный вагон; 2- приемный бункер; 3 - щековая дробилка; 4 - элеватор; 5 - сушильный барабан; б - дробилка; 7 - сито; 8 - ленточный конвейер; 9 - отстойник; 10 - бункер сырья; 11 - весы; 12 - смеситель шихты; 13 - бункер шихты; 14 - кюбель; 15 - циклон ЦН-15; 16 - пылеуловитель ГДП-М.
На рис.5.16 показан один из вариантов принципиальной схемы комплексной очистки технологических выбросов дозировочно-смесительных отделений. Уловленная циклоном пыль возвращается в расходный бункер соответствующего сырьевого материала. Шлам, образующийся при работе мокрого пылеуловителя, отстаивается и высушивается, после чего может использоваться как добавка к шихте после корректировки ее состава. Осветленная вода из отстойника возвращается на повторное использование в пылеуловитель.
Показатели, характеризующие эффективность схемы очистки (содержание пыли в очищаемых газах снижается до нормируемых пределов), приведены в табл . 5.6.
Таблица 5.6
Эффективность комбинированной схемы очистки
| Технологический процесс | Количество очищаемого воздуха, м3/ч | Запыленность г/м3 | Степень очистки, % | |||
на входе | после циклонов ЦН-15 | на выходе | циклоном ЦН-15 | пылеуловителем ГДП-М | |||
Песок | Сушка | 6,5 | 0,036 | 78,3 | 99,38 | ||
Просеивание | 21,4 | 5,1 | 0,016 | 76,1 | 99,68 | ||
Дробление и сушка | 18,3 | 5,8 | 0,042 | 68,3 | 99,2 | ||
Доломит | Просеивание | 21,9 | 4,8 | 0,018 | 99,6 | ||
Мел | Сушка | 14,9 | 3.9 | 0,066 | 73,8 | 98,3 | |
Карбонат натрия | Пневмотранспортирование | 5,6 | 2,5 | 0,023 | 55,4 | 99,08 | |
Содо-суль- фатная смесь | Сушка | 21,8 | 6,1 | 0,023 | 99,62 | ||
Сырьевые компоненты | Просеивание | 22,8 | 4,3 | 0,014 | 99,67 | ||
Транспортирование и смешивание | 3,6 | 0,012 | 99,66 | ||||
Рекомендуемые режимные параметры и варианты комбинаций аппаратов для других схем очистки газов от пылей приведены в таблице 5.7.
Таблица 5.7
Режимные параметры и варианты комбинаций пылеулавливающих аппаратов
Материал | Обеспы- леваемое оборудование | Объем отходя- щих газов, м3/ч | Характеристика по группам классификации | Рекомен- дуемое число | Пылеуло- витель | ||||||
пылегазовый поток | пыль | ||||||||||
запыленность, г/м3 | температура, °с | точка росы, ос | основная фракция, % | смачиваемость, % | слипаемость, 102 Па (Н/м2) | удельное электрическое сопротивление, Ом м | ступеней очистки | ступень | |||
Пресс- порошок | Распыли- тельные сушилки | 6000- | 7,2-16,1 | 120-160 | 67-75 | <20 мкм 72-96 | Хорошо смачивае- мая, 94-98 | Неслипа- ющаяся, слабосли-пающаяся, 0-1.9 | Вторая группа (1 х 106-3,5x10е) | Аппарат мокрой очистки | |
Вращаю- щиеся печи | 16000- | 7,5-15,9 | 160-230 | 40-48 | >20 мкм 49-52 | Хорошо и средне- смачивае-мая, 50-86 | Неслипа- ющаяся, слабосли-пающаяся, 0-1,2 | Третья группа (6x109-5х1010) | Аппарат сухой очистки | ||
Шамот | Шахтная печь (разгрузка) | 1,1 | 1,55 | Неслипа-ющаяся | 7х109 | То же | |||||
Шлак | Газоструйная мельница | 185-236 | <20 мкм | Хорошо омачиваемая, | Слабосли-пающаяся, 0,95 | Третья группа (1 х10 ) | Аппарат мокрой очистки | ||||
Глина | Сушиль- ный барабан | 35000- | 13,6-15,0 | 155-225 | 40-53 | >20 мкм 52-72 | Хорошо смачивае- мая, | Неслипа- ющаяся | Третья группа | То же |
ЛИТЕРАТУРА
1. Н.Е. Николайкина, Н.И. Николайкин, А.М. Матягина. Промышленная экология: Инженерная защита биосферы от воздействия воздушного транспорта: Учеб. пособие. М.: ИКЦ "Академкнига", 2006.- 239 с.
2. Техника и технология защиты воздушной среды: Уч. пос. для ВУЗов /В.В. Юшин, В.М. Попов, П.П. Кукин и др. – М.: В. школа, 2005. – 391 с.
3. Оборудование, сооружения, основы проектирования химико-технологических процессов защиты биосферы от промышленных выбросов /Л.И. Родионов, Ю.П. Кузнецов, В.В. Зенков, Г.С. Соловьев. М.: Химия, 1985. 352 с.
4. Степанов Г.Ю. Зицер И.М. Инерционные воздухоочистители М.: Машиностроение, 1986. 184 с.
5. Охрана окружающей среды /С.В. Белов, Ф.А. Барбинов, А.Ф. Козьяков и др. М.: Высшая школа, 1991. 319 с.
Лекция 6
ОЧИСТКА И ПОВТОРНОЕ ИСПОЛЬЗОВАНИЕ ТЕХНИЧЕСКОЙ ВОДЫ И ПРОМЫШЛЕННЫХ СТОКОВ
В процессах эксплуатации промышленного оборудования образуются сточные воды, которые требуют специальной очистки перед сбросом в канализационные системы. Наиболее распространенными загрязняющими веществами в поверхностных водах являются нефтепродукты, фенолы, легкоокисляемые органические вещества, соединения меди, цинка, аммонийный и нитратный азот, лигнин, ксантогенаты, анилин, метилмеркаптан, формальдегид и др. Например, сточные воды заводов черной и цветной металлургии загрязнены большим количеством взвешенных минеральных веществ, содержат цветные металлы и железо, сульфаты, хлориды, смолы и масла, серную кислоту, железный купорос. Нефтеперерабатывающие заводы и нефтепромыслы сбрасывают нефть и нефтепродукты, хлориды, взвешенные вещества, возможно присутствие железа и сероводорода. Большую опасность представляют сточные воды коксохимических предприятий: смолы, масла, фенолы, аммиак, цианиды, роданиды, большое количество солей неорганических кислот и взвешенных веществ. К сильно загрязненным сточным водам, трудно поддающимся очистке, относятся жидкие стоки целлюлозно-бумажных комбинатов: растворенные органические вещества, волокно, каолин и др. Машиностроительные и автомобильные заводы сбрасывают цианиды, хром, масла и окалину. Основные загрязнители текстильных предприятий - красители и СПАВ [1].