Лекция №2. Листопрокатное производство. Производство горячекатаной листовой стали. Производство холоднокатаной листовой стали
Конспект лекционных занятий
Лекция №1. Введение. Классификация процессов ОМД. Металлы и сплавы, используемые для изготовления изделий методами ОМД. Перспективы развития металлообработки. Прокатное производство
Детали машин, сооружений и другие изделия современной техники изготовляются главным образом из металлов и их сплавов на металлургических и машиностроительных заводах.
Основными методами изготовления металлических деталей и их полуфабрикатов являются литье, обработка давлением и обработка резанием. Особое место занимает обработка металлов давлением (ОМД), заключающаяся в пластическом изменении формы металла посредством его деформирования.
Обработка давлением позволяет получать детали или их полуфабрикаты в виде заготовок, близких по форме к готовым деталям, с большой производительностью и малыми отходами. Металл подвергается пластической деформации как в холодном, так и в горячем состоянии. В процессе пластического деформирования изменяется структура металла и повышаются его механические свойства. Поэтому наиболее тяжелонагруженные детали машин изготовляются обработкой давлением.
Пластическое деформирование осуществляется различными способами, к числу которых относятся прокатка, свободная ковка, объемная штамповка, прессование, волочение, листовая штамповка и специализированные виды ОМД (рисунок 1.1).
Вследствие возможности формообразования металла с высокой производительностью и малыми отходами, а также возможности повышения его механических свойств значение обработки давлением в современной промышленности огромно.
Обработка металлов давлением в целом является заготовительной базой машиностроения и металлургии. В конечном счете от ее качественного развития и совершенствования зависят создание мощных энергетических установок, новых летательных аппаратов, современных автомобилей и грузоподъемных машин, новейшей электронной и космической техники.
Экономия металла – одна из основных задач стоящих перед ОМД. Для оценки экономических показателей используют численное отношение массы детали к массе израсходованного на него металла, называемое коэффициентом использования металла (КИМ) и выраженное в процентах. Самое большое значения КИМ иметь холодная объемная штамповка и прокатка (82 и 85 %).
Процессы металлообработки, и в частности ОМД, будут развиваться в направлении создания экономически более выгодных методов обработки, какими в первую очередь являются комбинированные и совмещенные процессы. При этом сокращение металлургических переделов связано с организацией непрерывных технологических схем производства. Это приведет к значительному снижению трудоемкости и энергоемкости процессов, к снижению отходов и увеличению выхода годного металла.
Рисунок 1.1 – Классификация процессов ОМД
В качестве исходного материала в обработке металлов давлением применяют стали всех марок, алюминиевые, магниевые, титановые сплавы, а также сплавы на основе меди и никеля в виде слитков, прутков, различных сортовых профилей и т. д. Для ковки, например, используют спокойную сталь, раскисляемую полностью до разливки. Кипящая сталь менее пригодна для ковки, т. к. в слитках из нее трудно обеспечить полную заварку пустот и пузырей в процессе деформации. После прокатки эту сталь используют для штамповки.
Для обеспечения необходимых пластических свойств металлы и сплавы деформируются как в холодном, так и (преимущественно) в горячем состоянии.
Стали, сплавы железа с углеродом (до 2,14 %) используются практически во всех отраслях промышленности, машиностроении, металлургии, строительстве, автомобилестроении и т.п. В зависимости от химического состава сталь бывает углеродистая ( Ст3, 08 кп) и легированная (3Х2В8Ф, 5ХНМ); от назначения – конструкционная и инструментальная; от способа получения – мартеновская, бессемеровская, томасовская; от способа раскисления – спокойная, полуспокойная и кипящая. Углеродистые стали подразделяют на низкоуглеродистые (до 0,25 % углерода), среднеуглеродистые (0,25–0,60 %) и высокоуглеродистые (свыше 0,6). Низко- и среднеуглеродистые стали являются конструкционными, а высокоуглеродистые – инструментальными. Они имеют большой запас пластичности и могут деформироваться со степенями деформации до 80 %. Стали высокоуглеродистые и высоколегированные допускают деформацию за один цикл обработки не более 60 %, поэтому их относят к материалам средней пластичности.
Для алюминиевых сплавов характерен малый удельный вес и высокие прочностные свойства. Их подразделяют на мягкие сплавы (АМц, АД31, АМГ), сплавы средней твердости (Д1, Д16, АК1) и высокой прочности (АК8, В95). Кроме того, различают термически упрочняемые и термически неупрочняемые сплавы. Алюминиевые сплавы обладают высокой пластичностью, что дает возможность прессованием на горизонтальных гидравлических прессах получать самые разнообразные профили очень сложных конфигураций и различных сечений. Такие свойства алюминиевых сплавов, как низкая плотность, высокая коррозионная стойкость, сравнительно высокие механические свойства, позволяют применять изделия из них в различных деталях машин, автомобилестроении, в строительных конструкциях и архитектурных сооружениях. Основными потребителями сплошных и полых профилей из алюминиевых сплавов является авиационная промышленность, судостроение, холодильная техника, электротехническая промышленность, радиолокация. В последние годы сортамент полых профилей из алюминиевых сплавов значительно увеличился благодаря их использованию в строительстве для изготовления отделочных и конструкционных строительных деталей (детали оконных витражей, перегородок, подвесных потолков, рам, внутренних карнизов, встроенной мебели и др.).
Медь и сплавы на ее основе широко используются во многих отраслях промышленности: электротехнической, строительной, теплоэнергетической. Медь обладает хорошей пластичностью, поэтому из нее изготавливают детали практически всеми способами ОМД. Выделяют две группы сплавов – бронзы и латуни. Латуни (сплавы меди с цинком), обрабатываемые давлением, подразделяются более чем на 8 марок. Для горячей обработки металлов давлением широко применяют латуни марок Л62 и Л68. Бронзы (сплавы меди с оловом, алюминием, марганцем, кремнием, бериллием и другими элементами, кроме цинка) подразделяют на 10 марок. Безоловянистые бронзы характеризуются хорошими антифрикционными и антикоррозионными свойствами, могут работать в соленой воде, масле, паре. Магниевые сплавы (МА2, МА5, ВМ 65-1) относятся к легким сплавам и обладают склонностью к повышенной коррозии, вследствие чего имеют ограниченное применение в машиностроении. В основном, их используют в авиационной промышленности в качестве конструкционных материалов. Область применения – ракето- и самолетостроение, автомобилестроение, электротехническая промышленность.
Титановые сплавы (ВТ1-1) обладают наибольшей удельной прочностью, высокой антикоррозионной стойкостью и жаропрочностью. Находят применение в авиастроении, химическом и транспортном машиностроении, их используют для изготовления поковок для ракет, самолетов (турбинные лопатки), обшивки для подводных лодок, кислотоупорных деталей.
Кроме перечисленных в различных отраслях народного хозяйства широко используются и другие металлы и сплавы. Например, для производства ювелирных изделий применяют такие известные металлы, как золото, платина, палладий, серебро и сплавы на их основе. Для электротехнической промышленности используют сплавы тугоплавких металлов, таких как вольфрам, молибден и др. Кроме того, в качестве декоративных сплавов используются медноникелелевые сплавы такие, например, как мельхиор (МН19), нейзильбер (НМЖМц26-2,5-1,5) и др.
В качестве перспектив развития металлообработки методами ОМД выделим следующие: всесторонняя механизация и автоматизация процессов обработки металлов давлением: создание новых непрерывных процессов совмещенной обработки черных и цветных металлов и их сплавов; увеличение мощностей производственного оборудования и их производительности; реализация малоотходных и безотходных технологий производства изделий методами ОМД; применение современных программных средств для проектирования и управления технологическими процессами ОМД; разработка новых материалов, видов оборудования и технологий для обработки труднодеформируемых и малопластичных сплавов; разработка систем автоматизированного проектирования (САПР) технологии и инструмента для процессов ОМД.
Прокатное производство – это комплекс взаимосвязанных технологических переделов, определяющих качество прокатной продукции и технико-экономические показатели прокатного цеха. Развитие прокатного производства базируется на использовании нового, более совершенного нагревательного, прокатного и отделочного оборудования, характеризующегося поточностью ряда технологических процессов и операций, более высокими скоростями и интенсивным режимом работы. Решающим направлением технического прогресса в прокатном производстве является комплексная механизация и автоматизация производственных процессов, расширение сортамента продукции, повышение ее качества и экономии металла.
Выделяют производство проката из черных и цветных металлов, причем производство проката из сталей занимает превалирующее положение. При производстве проката из цветных металлов и сплавов большую долю в объеме занимает листопрокатное производство.
Прокатка металлов является таким видом пластической обработки, когда исходная заготовка обжимается вращающимися валками прокатного стана в целях уменьшения поперечного сечения заготовки и придания ей заданной формы. Существует три основных способа прокатки (рисунок 1.2): продольная (рисунок 1.2, а), поперечная (рисунок 1.2, б) и поперечно-винтовая (или косая) (рисунок 1.2, в).
а – продольная; б – поперечная; в – поперечно-винтовая: 1 – правый валок; 2 – заготовка; 3 – левый валок; 4 – гильза; 5 – оправка; 6 – штанга (стержень)
Рисунок 1.2 – Схемы прокатки
При продольной прокатке деформирование заготовки 2 осуществляется между вращающимися в разные стороны валками 7 и 3. Из простейшей схемы поперечной прокатки видно, что оси прокатных валков 1 и 3 и обрабатываемой заготовки 2 параллельны (или пересекаются под небольшим углом). Оба валка вращаются в одном направлении, а заготовка круглого сечения – в противоположном.
В процессе поперечной прокатки обрабатываемая заготовка удерживается в валках с помощью специального приспособления. Обжатие заготовки по диаметру и придание ей требуемой формы сечения обеспечиваются соответствующей профилировкой валков и изменением расстояния между ними. Данным способом производят изделия, представляющие собой тела вращения (шары, оси, шестерни и пр.).
Поперечно-винтовая, или косая прокатка, выполняется во вращающихся в одном направлении валках, установленных в прокатной клети под некоторым углом друг к другу (рисунок 1.2). Станы косой прокатки используют при производстве труб, главным образом, для прошивки слитка или заготовки в гильзу. В момент соприкосновения металла с вращающимися валками, имеющими наклон к оси обрабатываемой заготовки, возникают силы, направленные вдоль оси заготовки, и силы, направленные по касательной к ее поперечному сечению. Совместное действие этих сил обеспечивает вращение, втягивание обрабатываемой заготовки в суживающую щель и деформирование.
Различают листовую и сортовую прокатку. При сортовой прокатке на бочке валков имеются ручьи, образующие при составлении двух и более валков калибр по форме и размерам получаемого полуфабриката. При листовой прокатке применяется гладкая бочка валков.
Наиболее распространенной является прокатка на станах « Дуо» и «Трио», клети которых содержат, соответственно, два и три рабочих валка. Для производства тонколистового проката и фольги используется многовалковая прокатка. В этом случае прокатка осуществляется в клетях с четырьмя (Кварто), шестью, двенадцатью и двадцатью валками. Универсальные клети содержат, как правило, два вертикальных и два горизонтальных валка, образующих закрытый калибр по форме и размерам готового проката.
Продукция прокатного производства. Продукция прокатного производства имеет очень широкое применение во всех отраслях народного хозяйства. Она используется в виде заготовок различного профиля для изготовления деталей машин, станков, тракторов, автомобилей, паровозов, вагонов, железнодорожных путей; для строительства зданий, мостов и других сооружений. Указанные машины и сооружения изготовляются из прокатных черных и цветных металлов и их сплавов
Сортамент прокатных профилей. Профилем проката называется форма его поперечного сечения, сортаментом – совокупность профилей с различными размерами, получаемых прокаткой на одном стане или на группе станов. Сортамент прокатываемых профилей весьма разнообразен. Его разделяют на пять основных групп: 1) сортовой прокат; 2) листовой прокат; 3) трубы; 4) специальные виды проката (колеса, бандажи, кольца и др.); 5) периодический прокат.
Профиль сортового металла разделяют на две группы: простой геометрической формы (квадратная, круглая и полосовая сталь) и сложной – фасонной формы (двутавровые балки, швеллеры, зетовая сталь, рельсы и др.).
Листовой прокат (сталь) разделяют на толстолистовую сталь (толщиной более 4 мм), тонколистовую (толщиной менее 4 мм) и широкополосную, или универсальную сталь. Листы толщиной от 3 до 8 мм часто называют листами средней толщины. Толстолистовая сталь имеет ширину от 600 до 5000 мм при толщине от 4 до 160 мм и длине от 4 до 12 м. Броневые плиты имеют ширину до 4500 мм и толщину до 550 мм.
Тонколистовая сталь имеет ширину от 500 до 2500 мм, толщину от 0,20 до 3,75 мм и длину от 700 до 4000 мм. Листы (лента) толщиной меньше 0,20 мм носят название фольги. Листы должны быть с обрезанными кромками. Электротехническая и трансформаторная стали имеют ширину 750 и 1000 мм и толщину от 0,35 до 1,0 мм.
Широкополосная, или универсальная сталь, имеет ширину от 200 до 1500 мм при толщине от 4 до 60 мм. Тонкие стальные ленты изготовляются шириной от 20 до 2500 мм и длиной до 300 м в зависимости от толщины.
Трубы стальные подразделяются на две группы: бесшовные с диаметром от 25 до 600 мм и сварные – встык, внакладку и холоднопрофилированные – с диаметром от 10 до 1400 мм.
Периодический прокат представляет собой заготовку, поперечное сечение которой не остается одинаковым по форме и площади, а периодически изменяется.
Цветные металлы и их сплавы прокатываются преимущественно на простые профили – квадратный, круглый, полосовой (прямоугольный) в виде листов и лент различных размеров: по толщине от 0,2 до 25–30 мм, по ширине – листы до 3000 мм, ленты до 600 мм (и больше); по длине – листы до 6 м, ленты до 300 м и больше в зависимости от толщины.
В качестве технологических характеристик прокатки используют такие показатели, как производительность и скорость прокатки, степень деформации (обжатия) за один проход и вытяжка. В общем случае основным показателем степени деформации при прокатке является вытяжка λ = Fо/F1, которая определяется как отношение площади поперечного сечения заготовки F0 к площади поперечного сечения готового изделия F1. В частном случае, например при листовой прокатке без уширения, вытяжку определяют как отношение длин заготовки и изделия. Величину Δ H = H0− H1 называют абсолютным обжатием, а величину εh = (ΔH/H0)⋅100% – относительным обжатием (здесь H0 и H1 – соответственно, высота полуфабриката до и после деформации). Производительность прокатного стана, т/ч, можно рассчитать по формуле A = (3600/tц)G, где G – масса заготовки (слитка), т; tц – время (цикл) прокатки, с.
Производство листового проката (листов, лент) осуществляется методами горячей (толстолистовой материал) и холодной прокатки (тонколистовой материал, фольга). Горячую прокатку ведут на двух-, трех- или четырехвалковых станах листовой прокатки. Наиболее современным оборудованием являются непрерывные широкополосные станы. Исходным материалом являются слябы массой от 7,5 до 45 т, нагреваемые в методических печах. Холодную прокатку стали с минимальной толщиной 0,15 мм ведут на четырех-шестиклетьевых непрерывных станах или на станах «Кварто», оснащенных моталками (для рулонной прокатки). Для производства алюминиевой фольги применяют непрерывнолитую заготовку, которую прокатывают с толщины 6 мм на станах «Кварто» до микронных размеров.
Для производства листового и сортового проката в прокатных цехах устанавливают станы различного типа и назначения. Условно выделяют несколько групп.
1. Заготовочные станы: блюминги, слябинги, непрерывные заготовочные станы. Блюминги и слябинги – это крупные обжимные станы с диаметром валков 850–1500 мм, в которых прокатку ведут за 11–15 проходов в реверсивном режиме. Как правило, это одноклетьевые станы для производства заготовок больших размеров в виде прямоугольной заготовки (сляба) и квадратной заготовки (блюма). Непрерывные заготовочные станы устанавливаются непосредственно за блюмингом (слябингом) и имеют обычно две непрерывные группы по шесть клетей в каждой.
2. Станы для производства готового проката: сортовые, листовые, трубные и специальные. К сортовым станам относят крупносортные, рельсобалочные, средне- и мелкосортные. К листовым станам относят станы для прокатки толстолистовой и тонколистовой (рулонной) прокатки. К трубным станам относят прошивные, раскатные станы и станы холодной прокатки труб (ХПТ), а также станы для получения сварных труб. К специальным станам относят станы для прокатки периодических, гнутых профилей, шаропрокатные, колесопрокатные и другие станы.
За основной параметр у сортопрокатных станов принимают диаметр рабочих валков. Например, обозначение стан «Кварто 400» означает, что стан имеет 4 валка, из которых 2 опорных и 2 рабочих диаметром 400 мм. У листовых станов за основной параметр принята длина бочки валков, поэтому обозначение «стан 2000» означает, что у данного стана длина бочки валков составляет 2000 мм.
По расположению рабочих клетей выделяют следующие виды прокатных станов: одноклетьевые, линейные, многоклетьевые, последовательные, полунепрерывные и непрерывные.
Калибровкой валков называют последовательность калибров, расположенных на валках прокатного стана и обеспечивающих получение профиля заданных размеров. В каждом калибре в зависимости от типа стана металл прокатывают за один или несколько проходов, в результате чего заготовка превращается в раскат требуемого сечения. В понятие калибровки включают также определение формы и размеров калибров и размещение их на валках прокатного стана (т. е. процесс проектирования калибровки валков).
Калибры подразделяются на двухвалковые и многовалковые, причем некоторые калибры одинаковой формы могут быть образованы двумя и более валками. В практике прокатного производства нашли применение двухвалковые, трехвалковые и четырехвалковые калибры (рисунок 1.3).
Калибры классифицируются по форме, расположению на валках и назначению. По форме калибры подразделяют на две основные группы: простой формы (ящичные или прямоугольные, ромбические, шестиугольные, овальные, круглые, квадратные, шестигранные) и фасонные (балочные, швеллерные, уголковые, рельсовые, тавровые и др.).
а – вырезов 1; б – выступов 2; в – выреза 1 и выступа 2; г – вырезов 1 и выступа 2
Рисунок 1.3 – Калибры, образованные ручьями в виде
По расположению в валках различают калибры открытые, закрытые, полузакрытые и диагональные. У открытых калибров горизонтальный зазор между буртами валков располагается приблизительно посередине высоты калибра, у закрытых – за пределами калибра, у полузакрытых – ближе к основанию или вершине калибра, у диагональных зазоры между буртами располагаются по диагонали (например, у левого бурта в нижней, а у правого – в верхней части калибра).
По назначению калибры подразделяют на обжимные, черновые, предчистовые и чистовые. Обжимные калибры предназначены для уменьшения площади поперечного сечения исходного слитка, блюма или заготовки с целью получения заготовки, из которой в дальнейшем будет формироваться требуемый профиль. В качестве обжимных обычно используют ящичные калибры. Эти калибры применяют при прокатке на блюмингах и заготовочных станах, а также в первых проходах на сортовых станах. Черновые калибры предназначены для постепенного формирования прокатываемого фасонного профиля (например, двутавровой балки, швеллера и т. д.). На сортовых станах черновые калибры располагаются после обжимных калибров. При прокатке простых сортовых профилей (круг, квадрат, шестигранник) к черновым относят калибры простой формы, в которых производится дальнейшее уменьшение площади поперечного сечения раската, причем эти калибры располагаются в такой последовательности, чтобы обеспечить максимальную вытяжку, т. е. используются как вытяжные. Черновые калибры применяются в черновых и промежуточных группах клетей стана (рисунок 1.4).
|
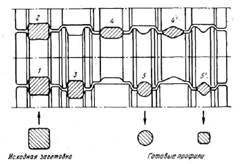
Металлургический завод с полным металлургическим циклом, производящий металл в том или другом виде из исходных материалов, включает в свой состав следующие цехи, которые обеспечивают производство и обработку различных видов изделий: доменные (производство чугуна); мартеновские, конвертерные, электросталеплавильные (производство стали и других металлов); цехи горячей прокатки (горячекатаный прокат и трубы); цехи холодной прокатки (производство холоднокатаных листов, лент и труб, отличающихся высокой точностью размеров по толщине, высокой степенью отделки поверхности, а также дополнительными физико-механическими характеристиками); калибровочные цехи (производство калиброванного металла в прутках и бунтах с высоким качеством поверхности и высокими допусками по размерам); цехи антикоррозионных и других видов покрытий (лужение, оцинкование, алюминирование, хромирование и др.); цехи гнутых профилей (получение тонкостенных гнутых профилей широкого сортамента из листового проката); термические цехи и различные виды отделки металла. Поэтому доменные, сталеплавильные, прокатные и другие цехи при производстве металлов являются основными, ведущими цехами металлургического завода.
Если включить еще получение кокса, что обычно имеет место на металлургическом заводе полного цикла, то такое сочетание цехов является наиболее рациональным с точки зрения использования отходящих газов доменных и коксовых печей, теплоты жидкого чугуна при передаче его из доменного в сталеплавильные цехи и теплоты горячих слитков при передаче их из сталеплавильных в прокатные цехи и на отделку.
Длительное время получение готового проката выполнялось по технологической схеме слиток – готовый прокат (рисунок 1.5). В этих условиях получали слиток небольшой массы и выбирался он с таким расчетом, чтобы из него можно было получить необходимое изделие всего за один нагрев. Однако по мере развития машиностроения и металлургии, главным образом высокопроизводительных способов получения стали, возникла необходимость разливать сталь в слитки значительной массы – 6 – 10 т и более. Получение готового проката из такого слитка за один нагрев не всегда представляется возможным. По этой причине начали строить обжимные станы, задача которых состояла в обработке слитка в заготовку. Данное обстоятельство привело к новой технологической схеме: слиток – полупродукт (заготовка) – готовый прокат.
Поэтому прокатные цехи, как правило, имеют в своем составе обжимные (блюминги, слябинги) и заготовочные станы, являющиеся основными агрегатами, связывающими сталеплавильные цехи и прокатные станы, выпускающие готовый прокат; сортовые станы (рельсобалочные, крупно, средне-, мелкосортные и проволочные); листопрокатные станы; трубные станы и др.
Наряду с такой широко распространенной технологической схемой наблюдается переход к схеме литая заготовка – готовый прокат (рисунок 1.6). Этому способствует успешное освоение разливки стали в заготовки квадратного и прямоугольного сечений, что имело распространение лишь в цветной металлургии. Непрерывное литье стальных заготовок длительное время не применялось из-за значительных трудностей выполнения технологического процесса самой разливки. Однако этот процесс обеспечивает получение химически более однородной плотной заготовки, что резко повышает выход годного. Например, на слябах спокойной углеродистой стали выход годного выше на 20 %, чем при разливке в изложницы. Вместе с тем исключается необходимость иметь отделение подготовки изложниц и поддонов.
|
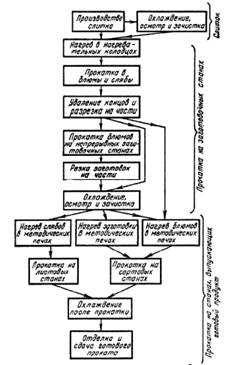
Применение непрерывной разливки стали снижает себестоимость металлургического передела, так как при этом устраняется необходимость в дорогостоящем оборудовании обжимных цехов, исключаются расходы на содержание обслуживающего и административного персонала. Установлено, что себестоимость проката в этих условиях снижается на 8–10 % при улучшении во многих случаях механических свойств и других характеристик стали. Кроме того, непрерывная разливка существенным образом меняет условия работы в сталеплавильных цехах, позволяет механизировать и автоматизировать все металлургическое производство: получение чугуна, стали, готового проката. Поэтому непрерывная разливка получает значительное развитие во всех странах.
|
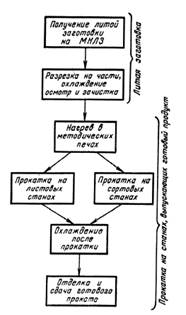
Для производства труб и специальных профилей применяют подобные технологические схемы, отличие заключается в стадии получения заготовки и особенностей процесса формоизменения. Так, при производстве бесшовных труб горячей прокаткой применяют прошивку заготовки в гильзу и раскатку гильзы в трубу с помощью метода поперечно-винтовой прокатки (см. рисунок 1.2). Для холодной прокатки бесшовных труб применяют станы ХПТ с периодическим режимом работы клети, когда клеть с валками перемещается, а заготовка обжимается валками с переменным радиусом
В данных схемах прокатки труб в качестве инструмента применяют конические оправки. При производстве сварных труб используют прокатку ленты (штрипса) в формовочно-сварочном стане, где в клетях с чередующимися горизонтальными и вертикальными валками полоса постепенно сворачивается и сваривается по длине. Специальные виды проката, к которым относят шары, оси, периодические профили и др., получают на станах поперечно-винтовой прокатки, имеющих различное число, форму и расположение рабочих валков.
Литература 1 осн. [3-8], 2 осн. [16-38].
Контрольные вопросы
1. В чем различие продольной и поперечной прокатки?
2. Для каких целей применяется сортовая прокатка?
3. С какой целью применяется многовалковая прокатка?
4. Что означает понятие «стан Кварто 400»?
5. Какой показатель характеризует степень деформации при прокатке?
6. Что такое калибровка прокатных валков?
Лекция №2. Листопрокатное производство. Производство горячекатаной листовой стали. Производство холоднокатаной листовой стали
Производство горячекатаной листовой стали.Листопрокатные станы рассмотрим как объекты, на которых осуществляется многоступенчатый процесс деформирования металла. Непрерывный широкополосный стан горячей прокатки состоит из двух групп клетей: черновой и чистовой. На рисунке 2.1 приведена схемы расположения основного оборудования широкополосных станов горячей прокатки.Черновая группа состоит обычно из отдельно стоящих клетей, расстояние между которыми больше длины раската. На некоторых станах последние два, три черновые клети объединены в непрерывную группу, что позволяет сократить длину стана. Чистовая группа состоит из 6 – 7 четырехвалковых клетей, прокатку в которых ведут одновременно, при этом образуется непрерывная группа. Скорости прокатки на непрерывных станах неуклонно возрастают, а длительность паузы между обжатиями в двух смежных клетях группы изменяется от нескольких секунд до десятых долей секунд в последних промежутках.
При прокатке непрерывных станах перепад температуры между первой и последней клетью достигает 270 °С. При этом, в последних клетях температура прокатки составляет 730 – 800 °С, а длительность пауз между деформациями незначительна. Это свидетельствует о создании условий для неполного прохождения разупрочняющих процессов в металле. Примерно такие же температурно-временные условия прокатки характерны для непрерывных штрипсовых станов, у которых расстояние между клетями меньше, чем у листовых станов, и составляет величину порядка 3,6 м, а скорость прокатки в последней клети достигает 21 м/с.
|
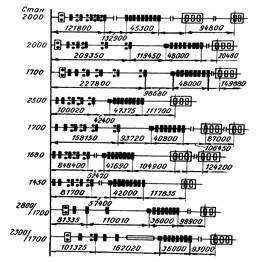
Толстолистовой стан 3600 (рисунок 2.2) предназначен для производства листов толщиной 5 – 50 мм, шириной 2000 – 3200 мм из слябов массой до 16 т и тяжелых плит (броневой стали) толщиной 50 – 200 мм и шириной 2000 – 3200 мм из слитков массой до 40 т. Слитки перед прокаткой нагревают в нагревательных колодцах либо в камерных печах с выдвижным подом. Слябы нагревают в пяти- и шестизонных методических печах с шагающими балками. Прокатку начинают в двухвалковой клети с вертикальными валками, где снимают конусность боковых граней слитка и разрушают слой окалины. Далее прокатку осуществляют в двух реверсивных четырехвалковых клетях, установленных последовательно. Рабочие валки клетей имеют диаметры 1100 и 1000 мм соответственно, а опорные 1800 мм. Привод каждой клети осуществляют два двигателя мощностью 6920 кВт на черновой и 8840 кВт – на чистовой. Скорость прокатки до 6 м/с. Использование двух четырехвалковых клетей позволяет уменьшить разнотолщинность по ширине листа. В черновой четырехвалковой клети при необходимости слиток или сляб поворачивают на 90° и прокатывают поперек для увеличения ширины до требуемой. За несколько проходов в каждой клети толщину раската уменьшают до заданной конечной. Для получения ровных боковых кромок и обеспечения точности листа по ширине чистовую клеть делают универсальной, т. е. с горизонтальными и вертикальными валками. Клети оборудованы устройствами для гидросбива окалины водой высокого давления (15 МПа).
После прокатки листы толщиной 5 – 50 мм поступают в роликовую закалочную машину для закалки или охлаждения до температуры 550 °С. Продольную и поперечную резку, в том числе на мерные длины до 12 м, осуществляют на гильотинных ножницах. Плиты после прокатки транспортируют тележками в пролеты замедленного охлаждения, огневой резки, термической обработки в камерных печах и зачистки. Годовая производительность стана 1,8 млн. т. толстых листов в год.
1 – 9 – оборудование для прокатки и отделки плит толщиной 50 – 200 мм: 1 - нагревательные колодцы; 2 – горизонтальный окалиноломатель; 3 – линейки манипулятора; 4 - двухвалковая клеть с вертикальными валками; 5 – черновая реверсивная четырехвалковая клеть 3600; 6 – сталкиватель плит; 7 – подъемно-опускающейся стол; 8 – передаточная тележка; 9 – камерная печи с выдвижным подом; 10 – 20 – оборудование для прокатки и отделки листов толщиной 5 – 50 мм: 10 – методические печи; 11 – чистовая реверсивная четырехвалковая клеть 3600; 12 – роликовая закалачная машина; 13 – ножницы поперечной резки; 14 – правильная машина; 15 – холодильник; 16 – охлаждающее устройство; 17 – роликовые печи для нормализации листов; 18 – дисковые ножницы для обрезки боковых кромок; 19 - кромкообрезные ножницы барабанного типа; 20 – печи для термообработки листов
Рисунок 2.2 – Схема расположение оборудования стана 3600
Для производства горячекатаной листовой стали толщиной от 1,2 до 16 мм и шириной до 2300 мм используют непрерывные широкополосовые станы (НШПС) производительностью 3,5 – 6,0 млн. т в год. Исходной заготовкой на таких станах служат слябы массой до 20 – 45 т, толщиной до 300 мм и шириной, равной ширине готового листа.
Значительную часть продукции НШПС составляют низко- и среднеуглеродистые конструкционные стали для штамповки деталей в автомобильной и других отраслях промышленности. Для обеспечения высокой пластичности и хорошей штампуемости горячекатаные листы должны иметь минимальную разнотолщинность по ширине и длине, а также определенные механические свойства и микроструктуру: однородное некрупное зерно феррита с равномерно распределенными в его поле мелкими частицами карбидов (цементита). Поскольку в ходе горячей прокатки протекают процессы рекристаллизации, то получение требуемых механических свойств и микроструктуры обеспечивается правильным выбором необходимой температуры конца прокатки (выше точки Ас3) и обжатия в последней клети. На диаграмме рекристаллизации стали видно, что при определенных сочетаниях обжатий и температур возникает крупное зерно, которое при штамповке вызывает шероховатость поверхности («апельсиновая корка») и в некоторых случаях брак по разрывам. При низкой температуре конца прокатки одновременно протекают два процесса – фазовое превращение аустенита в феррит и рекристаллизация деформированного феррита. Микроструктура металла после прокатки в этом случае состоит из неравномерных по величине зерен, а в некоторых случаях, когда времени от конца прокатки до остывания полосы недостаточно для полного протекания процесса рекристаллизации, в ней сохраняются следы наклепа, что при последующей штамповке вызывает неравномерную вытяжку детали.
Большое значение имеет также температура, при которой прокатанный лист сматывают в рулон. При высокой температуре смотки и медленном охлаждений рулона выделяются крупные включения цементита, резко увеличивающие склонность стали к разрывам при штамповке.
Рассмотренные выше требования к качеству горячекатаного листа предопределили характер технологического процесса и принципиальную конструкцию прокатных станов. Современные непрерывные широкополосовые станы горячей прокатки имеют две группы клетей: черновую и непрерывную чистовую. Использование четырехвалковых клетей позволяет значительно уменьшить разнотолщинность по длине и ширине полосы, а вертикальные валки универсальных клетей черновой группы обжимают боковые грани полосы, предотвращая образование выпуклости и, как следствие, разрывов кромок листа при прокатке. За чистовой группой клетей ниже уровня пола устанавливают вертикальные моталки для смотки полосы в рулоны. Между черновой и чистовой группами клетей, а также между чистовой группой и моталками расположены промежуточный и отводящий рольганги, предназначенные для транспортировки полосы и регулирования температурного режима ее прокатки и смотки. Если температура полосы выше необходимой, ее охлаждают на рольганге, который оборудован воздухо- или водоохлаждающим устройством с давлением воды 1 – 1,2 МПа. По требованию стандартов поверхность листов должна быть гладкой, без вкатанной печной и воздушной окалины. С этой целью перед черновой и чистовой группами устанавливают специальные клети, называемые окалиноломателями, в которых при сравнительно небольших обжатиях (10 – 12%) окалина взламывается и удаляется водой под давлением 15 МПа. Установки гидросбива окалины размещены за окалиноломателями и между черновыми клетями.
Непрерывный широкополосовой стан 2000 (рисунок 2.3) предназначен для прокатки рулонной листовой стали толщиной 1,2 – 12 мм. Литые и катаные слябы толщиной до 300 мм и массой 15 – 20 т из углеродистых и низколегированных сталей нагревают в четырех пятизонных методических печах 1до температуры 1150 – 1280 °С. Нагретый сляб поступает в черновую группу, состоящую из одной горизонтальной двухвалковой 3и четырех универсальных четырехвалковых клетей с горизонтальными валками диаметром 1180 (рабочие) и 1600 мм (опорные) и вертикальными валками диаметром 1000 мм. Перед группой установлен вертикальный окалиноломатель 2. Особенностью стана является объединение трех черновых клетей в непрерывную подгруппу 5, что позволило сократить длину и улучшить температурный режим прокатки за счет уменьшения потерь тепла.
1 – нагревательные печи; 2 – 5 – рабочие черновые клети; 2 – вертикальная черновая двухвалковая клеть – окалиноломатель; 3 – двухвалковая клеть; 4 – универсальная четырехвалковая клеть; 5 – непрерывная трехклетевая подгруппа универсальных четырехвалковых клетей; 6 – промежуточный рольганг; 7 – летучие барабанные ножницы; 8 – чистовой окалиноломатель; 9 – непрерывная чистовая группа; 10 – отводящие душирующие рольганги; 11 – моталки для полосы толщиной 1,2 – 4 мм; 12 – тележки с кантователем рулонов; 13 – моталки для полосы толщиной 4 – 16 мм; 14 – поворотный стол для рулонов; 15 транспортеры рулонов
Рисунок 2.3 – Схема расположения оборудования непрерывного широкополосного стана 2000
Непрерывная чистовая группа включает семь четырехвалковых клетей с диаметром рабочих 800 и опорных валков 1600 мм. Предусмотрена возможность установки восьмой клети. С целью уменьшения разнотолщинности полосы в последних трех клетях применяют противоизгиб рабочих валков при помощи гидравлических устройств. Необходимые размеры и однородность зерен феррита обеспечиваются автоматическим регулированием температуры конца прокатки в пределах 840 – 900°С в зависимости от марки стана и толщины листа. Перед группой установлены летучие ножницы двухбарабанного типа, предназначенные для обрезки переднего и заднего концов полосы – подката. Все клети стана имеют индивидуальные приводы. После выхода из последней чистовой клети полоса охлаждается душирующим устройством до температуры 500 – 650 °С и сматывается в рулон на одной из пяти ролико-барабанных моталок. Прокатанную полосу подают в цех холодной прокатки или на отделку, которая включает разматывание рулона, поперечную резку и укладку листов в стопы, продольную резку, травление, нормализацию или закалку, правку и др. и выполняется на специальных непрерывных линиях.
Для контроля и регулирования технологического процесса стан оборудован системой датчиков для измерения и регистрации усилий, температуры, натяжения, бесконтактных измерителей толщины и ширины полосы, а также исполнительных механизмов для обработки управляющих воздействий. Локальные системы автоматизации нагрева, транспортировки, регулирования температурного режима и режима обжатий имеют оперативную связь с центральной управляющей ЭВМ. Производительность стана 6 млн. т в год.
Для производства горячекатаных листов широкого сортамента из высоколегированных и труднодеформируемых сталей используют полунепрерывные листовые станы, у которых вместо черновой группы установлены двухвалковая реверсивная черновая клеть и универсальная четырехвалковая клеть. Наличие реверсивной клети позволяет выбирать обжатия и число проходов в зависимости от физико-механических свойств прокатываемой стали. Производительность таких станов ограничивается 1,5 – 2 млн. т в год.
Производство холоднокатаной листовой стали. На станах холодной прокатки производят листовую сталь толщиной от 0,2 до 5 мм и шириной от 200 до 2300 мм. Значительную часть продукции станов холодной прокатки составляет конструкционная тонколистовая углеродистая сталь качественная и обыкновенного качества для холодной штамповки сложных и особосложных деталей толщиной от 0,5 до 5 мм и шириной от 500 до 2300 мм. Холодной прокаткой производят низколегированную и легированную сталь общего назначения, жесть толщиной от 0,05 до 0,5 мм, электротехническую сталь анизотропную (трансформаторную) и изотропную (динамную для электродвигателей) толщиной 0,1 – 0,5 мм и другие виды металлопродукции. Холоднокатаную сталь поставляют в листах длиной от 1 до 6 м и в рулонах.
Исходным материалом для холодной прокатки является горячекатаная листовая сталь толщиной 2,0 – 5,0 мм, поступающая в рулонах со станов горячей прокатки. Производство холоднокатаной стали включает несколько основных процессов.
Подготовку исходного материала к прокатке выполняют на непрерывных травильных агрегатах, где рулон разматывают, полосу правят и концы сваривают. Основная цель – удалить с поверхности горячекатаного листа окалину. Перегибанием полосы вокруг роликов и прокаткой с обжатием 3 – 8 % в дрессировочной клети окалина взламывается, а затем удаляется химическим или электрохимическим травлением в серной или соляной кислоте. В последние годы применяют механическое удаление окалины дробеметными установками. В линии агрегата установлены дисковые ножницы, которыми обрезают неровную боковую кромку, после чего полосу промасливают и сворачивают в рулон массой до 50 т, гильотинными ножницами вырезая сварочные швы. При необходимости в агрегат встраивают проходную печь для термической обработки. Более 90 % всего холоднокатаного металла прокатывают на непрерывных четырех- и пятиклетевых станах, оборудованных разматывателем со скребковым отгибателем и правильно-подающими роликами, четырехвалковыми рабочими клетями (ширина бочки 1200 – 2500 мм) и моталками. Рабочие валки каждой клети имеют индивидуальный привод от двигателей постоянного тока через редукторы.
Давление металла на валки при холодной прокатке значительно уменьшается благодаря применению рабочих валков малого диаметра, созданию переднего и заднего натяжения, а также подаче смазочно-охлаждающих жидкостей, использованию технологической смазки. Прокатка со смазкой уменьшает прогиб и упругую деформацию валков и, следовательно, обеспечивает возможность применения больших обжатий. Кроме того, смазка снижает расход энергии, уменьшает расход валков, повышает качество листа за счет уменьшения разнотолщинности и устранения налипания металла на валки, а также охлаждает валки. При холодной прокатке применяют водно-масляные эмульсии, в состав которых входят эмульсол (содержит до 40 % смазочно-активных компонентов типа пальмового масла и др.), эмульгаторы (сульфанат натрия, мыла жирных кислот) и присадки (животный жир) для повышения смазочных свойств.
Для получения тонких полос с малой разнотолщинностью исключительно большое значение имеет жесткость клети и стабильность процесса прокатки. Разнотолщинность по ширине холоднокатаной полосы обусловлена: изменением прогиба, износа и температурного расширения по длине бочки валка; изменением по ширине полосы факторов, влияющих на величину контактных напряжений, а через них на упругую отдачу валков, - разнотолщинности исходной заготовки (подката), натяжения, подачи смазки и т. д. Для уменьшения разнотолщинности по ширине листа валки профилируют при шлифовке, регулируют интенсивность подачи эмульсии по длине валков (тепловая профилировка валков) и применяют принудительный изгиб опорных и рабочих валков в ходе прокатки с помощью гидромеханических устройств. Максимальное усилие противоизгиба не превышает 30 % усилия прокатки.
Разнотолщинность по длине полосы обусловлена разнотолщинностью подката, колебаниями коэффициента трения и натяжения. Коэффициент трения при прокатке с жидкой смазкой заметно уменьшается при увеличении скорости прокатки (разгоне стана) и возрастает при торможении, т. е. зависит от скоростного режима.
Режим деформации оказывает значительное влияние на механические свойства и структуру листовой стали. В процессе холодной прокатки происходит дробление и вытягивание зерен вдоль направления прокатки. Последующий рекристаллизационный отжиг устраняет наклеп и позволяет получить необходимые механические свойства и равноосную структуру, если общее обжатие не меньше 45 – 50 %. На современных станах общее обжатие достигает 70 – 80 %, что позволяет снизить температуру отжига. При распределении общего обжатия по клетям непрерывного стана стремятся равномерно загрузить двигатели всех клетей и максимально использовать прочностные возможности оборудования. Для увеличения точности прокатки обжатия в последней клети снижают до 10 – 25 %.
Скоростным режимом непрерывного стана холодной прокатки предусмотрено значительное снижение скорости прокатки (до 0,4 – 1,0 м/с) в начале прокатки рулона, когда передний конец пропускают через валки всех клетей и направляют на барабан моталки. Затем скорость прокатки увеличивают до рабочей и вновь снижают при прохождении через валки заднего конца рулона. На ряде станов скорость понижают и при прохождении через валки сварочного шва. Поскольку большая часть полосы прокатывается с переменной скоростью, то это приводит к изменению условий трения, усилий, упругой деформации элементов клетей, а в конечном итоге – к изменению толщины полосы по ее длине.
Для управления толщиной полосы тонколистовые станы оборудуют системами автоматического регулирования толщины (САРТ). Системы оснащены ЭВМ, которые обрабатывают показания измерительных приборов (изменение толщины полосы, усилия прокатки, загрузки двигателя и т. п.) и рассчитывают скорость и величину обжатия для каждой клети стана. Значительное улучшение качества полосы достигается на станах бесконечной прокатки (рисунок 2.4), на которых в потоке перед станом концы рулонов, подготовленных для прокатки, свариваются. В результате сокращаются операции заправки переднего конца, скорость прокатки снижается только при прохождении через валки сварных швов, соответственно повышается производительность стана. Непрерывность процесса обеспечивается наличием петлевого накопителя. На выходе полосу разрезают летучими ножницами и сматывают в рулоны. Пятиклетевой стан холодной бесконечной прокатки 2030 прокатывает 2,5 млн. т в год тонколистовой холоднокатаной стали толщиной 0,4 – 2 мм, шириной до 1800 мм. Подобные непрерывные станы с пятью и шестью рабочими клетями, но с меньшей длиной бочки (1400 мм) применяют для прокатки жести.
1 – группа разматывателей; 2 – тянущие и правильные ролики; 3 – сварочная машина; 4 – накопитель полосы с четырьмя петлявыми тележками; 5 – натяжные ролики; 6 – входная часть для порулонной прокатки; 7 – устройство для измерения толщины; 8 - пятиклетевая непрерывная группа; 9 – ротационные ножницы; 10 – группа моталок
Рисунок 2.4 – Непрерывный пятиклетевой листовой стан 2030 бесконечной прокатки
Кроме непрерывных станов, для холодной прокатки листа применяют одноклетевые реверсивные станы (для прокатки рулонов разнообразного сортамента – по толщине, ширине, маркам и т. д.), причем тонкие полосы (толщиной 0,1 – 0,3 мм) и особо тонкие (толщиной 2 мкм) прокатывают на двадцативалковых станах. На реверсивных станах прокатку ведут в несколько проходов, поэтому с обеих сторон клети устанавливают барабанные моталки.
Рекристаллизационный отжиг после холодной прокатки проводят в муфельных колпаковых печах с защитной атмосферой, а в последнее время – в непрерывных печах башенного типа, значительно ускоряющих процесс отжига и улучшающих качество готовой полосы вследствие более равномерного распределения механических свойств по длине и ширине листа, уменьшения волнистости и коробоватости.
При отжиге низкоуглеродистой стали структуру с равноосными зернами феррита и равномерно распределенными мелкими сфероидизированными частицами цементита получают при температуре 540 – 600 °С. Однако при этой температуре рекристаллизация полностью протекает за 2 ч. При той же степени холодной деформации и температуре 700 °С рекристаллизация заканчивается через 5 мин, поэтому на практике температуру отжига в муфельной печи устанавливают в интервале 680 – 700 °С. Продолжительность отжига 6 – 8 ч. В камере нагрева непрерывных печей полосу нагревают до 700 – 730 °С.
Следующей после отжига технологической операцией является дрессировка, т. е. холодная прокатка без смазки с обжатием 0,5 – 3 %. Цель дрессировки – правка, проглаживание и поверхностное упрочнение листа для предотвращения образования грубых полос скольжения при холодной штамповке. Для дрессировки устанавливают специальные станы с рабочими валками диаметром около 500 мм. Для полос толщиной 0,1 – 0,5 мм применяют непрерывные двуклетевые станы; для полос большей толщины – одноклетевые станы. Дрессировку осуществляют, за один или несколько проходов после отжига.
Отделку и покрытие прокатанных листов различными материалами выполняют на специальных агрегатах продольной и поперечной резки. Холодные рулоны разматывают, боковые кромки обрезают дисковыми ножницами, полосу правят и разрезают на листы мерной длины летучими ножницами. После промасливания и контроля дефектов листы пакетируют и увязывают.
Покрытие холоднокатаных листов различными пластмассами, лаком, оловом (электролитическое лужение), цинком, алюминием, хромом осуществляют на специальных высокопроизводительных установках непрерывного действия (рисунок 2.5). Листы в зависимости от вида покрытия обладают высокой коррозионной стойкостью, электроизоляционными свойствами, хорошим внешним видом и широко применяют в быту и промышленностях.
1 – разматыватели; 2 –гильотинные ножницы; 3– сварочная машина; 4 – подающие ролики; 5 – ванна электролитического обезжиривания; 6– ванны травления и промывки; 7 – ванна электролитического покрытия полосы оловом; 8 – камера сушки; 9– камера пассивации;
10 – моталки; 11– летучие ножницы; 12– листоукладчик
Рисунок 2.5 – Схема агрегата непрерывного электролитического лужения
Лекция №3 Сортопрокатное производство. Производство сортовых профилей.Производство рельсов и балок
Производство сортовых профилей.В зависимости от размеров сортовые профили делят на крупный, средний, мелкий сорт и проволоку (катанку). Современные прокатные станы специализированы на производстве определенной группы профилеразмеров, что позволяет достигнуть высокой производительности и обеспечить требуемое стандартами качество. Это обстоятельство в большинстве случаев определяет размеры станов, их конструкцию и расположение оборудования. Различают крупно-, средне- и мелкосортные станы, а также проволочные станы. Кроме того, существуют станы специального назначения – рельсобалочные, штрипсовые, полосовые.
Большинство сортовых станов имеет примерно одинаковый технологический цикл: нагрев, прокатка, охлаждение, резка на мерные длины, маркировка и уборка.
На крупносортных станах прокатывают круглые и квадратные профили со стороной квадрата 80 – 300 мм, балки и швеллеры № 12 – 24. Диаметр валков крупносортных станов 550 – 800 мм. В настоящее время крупный сорт получают в основном на непрерывных и полунепрерывных станах.
Полунепрерывный стан 600 предназначен для прокатки круглых профилей (диаметром 50 – 120 мм), рельсов (масса одного метра до 24 кг), балок высотой 100 – 200 мм и других профилей из блюмов сечением 300×300 мм со скоростью 10 м/с. Производительность стана 1,6 млн. т/год. Блюмы нагревают в трех пятизонных двухрядных методических печах с нижним подогревом, а затем прокатывают в 17 клетях с индивидуальными приводами. Клети расположены в трех параллельных линиях, соединенных шлепперами. Выходящий из стана прокат режут на 10 пилах горячей резки, что обеспечивает высокий ритм прокатки. После порезки металл поступает на холодильник, оборудованный специальными кантователями для поворота рельсов, а затем на один из трех участков отделки (для рельсов, сортового проката и крупных профилей).
Наиболее современным является заготовочно-крупносортный стан 700, предназначенный для прокатки круглых профилей диаметром 80 – 180 мм, в том числе трубной заготовки и квадратной заготовки 70 – 110 мм из легированных сталей. Производительность стана 2,3 млн. т/год (рисунок 3.1). Непрерывнолитые блюмы 300×360 мм длиной 6 – 12 м нагревают в трех нагревательных печах с шагающими балками до 1200 – 1250 °С и после гидросбива окалины прокатывают в ящичных калибрах обжимной двухвалковой реверсивной клети 950. После удаления переднего конца на ножницах усилием 8 МН и обработки при необходимости на машине огневой зачистки (МОЗ) раскат прокатывают в первой непрерывной группе, где получают круглые профили диаметром 100 – 180 мм, а для получения более мелких профилей прокатку продолжают во второй непрерывной группе. В непрерывных труппах применяют вытяжные системы калибров овал – круг. Чередующиеся вертикальные и горизонтальные клети с валками диаметром 700 мм и специальной жесткой конструкцией станин имеют индивидуальные приводы мощностью 1350 кВт. Перевалку производят с заменой клетей в течение 5 мин. Каждая группа клетей имеет отводящий рольганг, на котором установлены стационарная и передвижные пилы горячей резки проката на длины 9 – 15 м.
После резки металл поступает к печам отжига или непосредственно на холодильник, где охлаждается до температуры порядка 80 °С и передается на промежуточный высотный склад. В отделении отделки прокат на поточных линиях подвергают дробеметной очистке от окалины, правке, контролю и зачистке поверхностных дефектов, резке на мерные длины, клеймению, взвешиванию, упаковке, обвязке в пакеты. Часть металла обрабатывают на бесцентрово-токарных станках для получения особоточных круглых профилей с повышенным качеством поверхности. Особенностями стана являются автоматизация прокатки с помощью ЭВМ на обжимной клети, автоматический контроль качества поверхности в технологическом потоке и точности проката, высокая степень механизации и поточность отделочных операций.
1– нагревательные печи; 2 – установка гидросбива окалины; 3 - манипуляторы и кантователи; 4 – обжимная реверсивная клеть 1000; 5 – машина огневой зачистки; 6 – стационарные ножницы горячей резки; 7 – первая группа клетей; 8– пилы горячей резки; 9 – клеймовочные машины; 10 – маятниковые ножницы; 11 – кантователь; 12 – вторая группа клетей; 13 – кривошипные ножницы; 14 - шлеппер для передачи металла в отделение отделки и к холодильникам
Рисунок 3.1 – Схема расположения оборудования заготовочно-крупносортного стана 700
На среднесортных станах прокатывают круглые и квадратные профили 30 – 80 мм, двутавровые, швеллерные, полосовые и другие фасонные профили. Диаметр валков среднесортных станов 300 – 600 мм. Иногда станы этой группы, которая наиболее обширна, дополнительно подразделяют на мелкосортно-среднесортные и среднесортно-балочные.
Новый непрерывный мелкосортно-среднесортный стан 350 предназначен для производства 1 млн. т круглых (12 – 75 мм), квадратных, шестигранных и полосовых (шириной до 120 мм) профилей из легированной стали (рисунок 3.2). Готовый прокат производят в прутках и в бунтах (диаметром до 40 мм). Квадратную заготовку сечением 170×170 мм, длиной 9 – 11 мм и массой до 2,45 т нагревают в двух печах с шагающим подом. После шестиклетевой черновой группы 630 маршрут прокатки разветвляется на две нитки. Для прокатки мелкого сорта (12 – 32 мм) раскат поступает в роликовую проходную печь, а затем в первую промежуточную четырехклетевую группу 500, вторую промежуточную восьмиклетевую группу 400 и чистовую шестиклетевую группу 350 (скорость прокатки до 20 м/с). Средний сорт (34 – 75 мм) прокатывают в параллельной линии, включающей две группы клетей: промежуточную 500 и чистовую 350, где скорость прокатки не превышает 8 м/с. Расположение клетей позволяет производить прокатку одновременно в двух линиях (полутораниточная прокатка) и осуществлять безостановочный переход с профиля на профиль перевалкой клетей одной из линий. После прокатки в каждой линии металл может поступать либо на холодильник (одновременно на разные стороны), либо к печам поточной термической обработки. С мелкосортной линии металл также можно подавать к моталкам с последующим охлаждением на крюковом конвейере. Следует отметить, что полутораниточная прокатка позволяет в 1,5 раза увеличить производительность стана и на 35 % снизить удельные капитальные вложения.
1 – нагревательные печи; 2 – установка гидросбива окалины; 3 – черновая группа клетей; 4 –проходная подогревательная печь; 5 – первая промежуточная мелкосортная группа клетей; 6 – летучие ножницы; 7 – вторая промежуточная группа клетей; 8 – чистовая мелкосортная группа клетей; 9 – промежуточная среднесортная группа клетей; 10 – чистая среднесортная группа клетей; 11, 12 – установки двухстадийного охлаждения; 13 –моталки; 14 – пластинчатый транспортер; 15 –крюковый конвейер; 16 – холодильник; 17 – установка для уборки бунтов
Рисунок 3.2 – Схема расположения оборудования непрерывного мелкосортно-среднесортного стана 350
Непрерывный среднесортно-балочный стан 450 (рисунок 3.3) предназначен для прокатки облегченных тонкостенных двутавровых балок и швеллеров с высотой стенки 160 – 300 мм (в стандартах используют обозначение № 16 – 30) с наклонными и параллельными полками, угловых профилей № 6 – 12, круглых профилей диаметром 30 – 60 мм и квадратных и шестигранных профилей эквивалентного сечения из углеродистой и низколегированной стали. Производительность стана 1,5 млн. т. Заготовки сечением от 150×150 до 200×100 мм, длиной 12 м и массой до 4,7 т нагревают в печах с шагающим подом до 1150 – 1220 °С. Черновые клети с валками 630×1000 мм расположены в трех непрерывных группах. Особенностью конструкции стана является применение комбинированных клетей (К), которые в зависимости от установки могут работать как горизонтальные (Г) или как вертикальные (В). Вторая клеть каждой черновой группы комбинированная и поэтому возможны чередование горизонтальных и вертикальных клетей при получении сортовых профилей в вытяжных системах для исключения кантовки и кантовка калибра на 180° при получении фасонных профилей в горизонтальных клетях для смены фланцев. Для кантовки на 90 и 45° перед каждой группой установлен кантователь.
Чистовая группа состоит из семи комбинированных клетей с валками 530×630 и 480×600. Четыре из этих клетей, в том числе чистовая, могут быть заменены универсальными с диаметром валков 900 (Г) и 700 мм (В). Скорость прокатки в последней клети 15 м/с. За последней клетью установлены летучие ножницы усилием 0,63 МН для порезки на длины холодильника. Холодильник двусторонний с разветвлением к ножницам-штампам для порезки фасонного проката на мерные длины без смятия профиля. Мелкосортную сталь (круглые и квадратные профили 8 – 30 мм, мелкие угловые полосовые и некоторые фасонные профили, арматурная сталь) и катанку (круглая сталь диаметром 5 – 11 в бунтах) до недавнего времени почти полностью производили на непрерывных мелкосортных и проволочных (для прокатки катанки) станах 250.
Мелкосортный стан 250 (рисунок 3.4) состоит из двух групп клетей. В черновой группе, в которую входит семь двухвалковых клетей, прокатывают одновременно (параллельно) две заготовки размером 80×80×120мм (проката в две нитки). Чистовая группа разделена на две линии, каждая из которых состоит из восьми клетей с вертикальными и горизонтальными валками. В чистовой группе прокатку ведут в одну нитку. После прокатки полоса поступает либо на моталки для сматывания в бунты с последующим охлаждением на крюковом конвейере, либо на холодильник, а затем на ножницы резки. В зависимости от сортамента производительность станов 250 составляет 550 – 700 тыс. т в год; брак 0,3 %, суммарный расходный коэффициент 1,035 – 1,04.
1 – нагревательные печи; 2 – ножницы горячей резки; 3 – кантователь; 4 – черновая группа клетей; 5 –летучие ножницы; 6 – чистовая группа клетей; 7 – холодильник; 8 – правильные машины; 9– карманы;10 – ножницы холодной резки; 11 – вязальные машины; 12 – карманы для готового профиля; К – комбинированные клети (могут работать как пои горизонтальном, так и при вертикальном положении валков); У – универсальные клети (с одновременным горизонтальным и вертикальным расположением валков); Г – горизонтальные клети
Рисунок 3.3 – Схема расположения оборудования непрерывного среднесортного стана 450
I – склад заготовок; II – пролет стана; III – электромашинный зал; 1 – вталкиватель; 2– выталкиватель; 3– нагревательная печь; 4 – ножницы; 5 – черновые клети первой группы; 6– роторные летучие ножницы для обрезки концов раската; 7 – черновые клети второй группы; 8 – предчистовые клети; 9– чистовые группы клетей; 10– моталки с неподвижным барабаном; 11 – муфельные транспортеры; 12 – крюковый конвейер
Рисунок 3.4 – Схема расположения оборудования непрерывного
проволочного стана 250
На проволочном стане 250(рисунок 3.5) прокатывают катанку 5 – 10 мм из заготовки сечением 80×80 мм, длиной 12 м и массой 600 кг. Прокатку в черновой 450 и первой промежуточной 320 группах ведут в четыре нитки, во второй промежуточной группе 320 – в две нитки и в чистовых группах 250 – в одну нитку. Скорость прокатки в чистовой группе до 40 м/с, и ее дальнейшее увеличение невозможно из-за появления значительных крутильных колебаний. За каждой чистовой группой установлено по две моталки с неподвижным барабаном для смотки катанки в бунты, которые затем охлаждают на крюковом конвейере. Производительность подобных станов достигает 800 тыс. т в год и более. Однако качество катанки достаточно низкое из-за неравномерности свойств по длине (вследствие различных условий охлаждения в бунте крайних и внутренних витков), значительного слоя окалины (вследствие длительного охлаждения внутренних витков бунта), низкой точности при четырехниточной прокатке.
Современные тенденции развития мелкосортно-проволочных станов определяются возросшими требованиями к качеству проката и стремлением повысить производительность агрегатов. Повышение точности проката достигается прокаткой без натяжения как источника случайных колебаний технологических параметров, а также снижением неточности прокатки. При многониточной прокатке разновременность входа в клети передних и задних концов раскатов и выхода из них изменяет полное усилие и соответственно упругую деформацию элементов клети и, как следствие, вызывает колебание вертикального размера профиля по длине полосы. Кроме того, при однониточной прокатке появляется возможность избежать кантование раската, используя чередование вертикальных и горизонтальных клетей. Упрощение привалковой арматуры снижает вероятность появления таких дефектов, как риски и царапины. Значительное увеличение сечения и массы заготовки позволяет не только повысить производительность прокатных станов, но и улучшить качество проката путем увеличения общей вытяжки, а следовательно, выкатываемости дефектов заготовки. Учитывая трудности отделки бунтовой стали, в современные станы включают специальное отделение для контроля и отделки заготовки.
Оснащение современных прокатных станов АСУ ТП позволило осуществить автоматический контроль качества поверхности в технологическом потоке и точности профиля за чистовыми клетями с последующей отсортировкой проката для повторного контроля и зачистки в отделении отделки вне потока. Кардинальным решением вопроса повышения точности проката является внедрение систем автоматизированного регулирования размеров прока